Can 3D Scanning Aid Value Engineering?
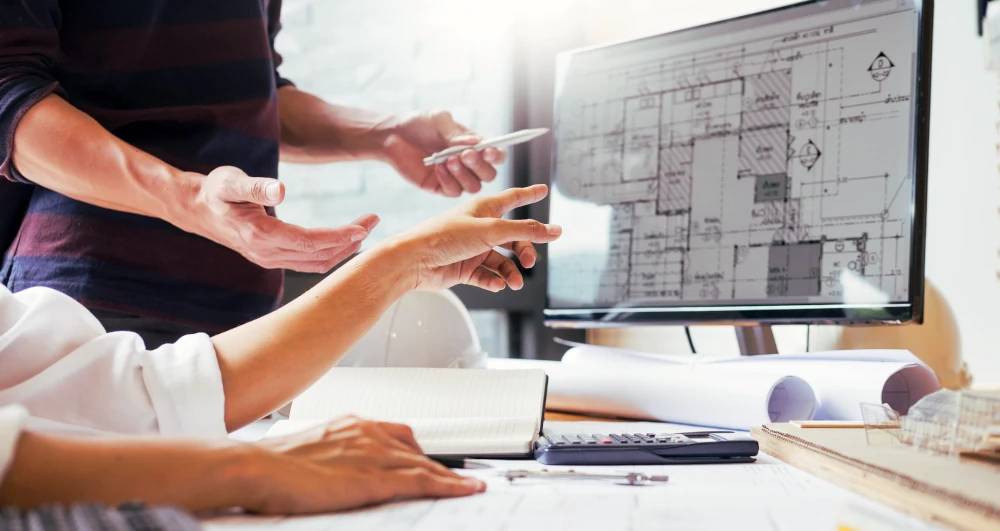
What is Value Engineering?
Value engineering is a systematic method for analyzing a project's components and functions to identify cost-effective solutions that maintain or enhance performance. This is achieved through alternatives in materials, design methods, or construction techniques that reduce costs while preserving functionality. The concept was first developed by Lawrence Miles at General Electric during World War II when material shortages required innovative design alternatives. Miles found that some substitutes not only reduced costs but also improved the product, leading to the creation of "value analysis," now known as value engineering. This methodology is widely used across industries to eliminate unnecessary costs, improve functionality, and enhance quality.
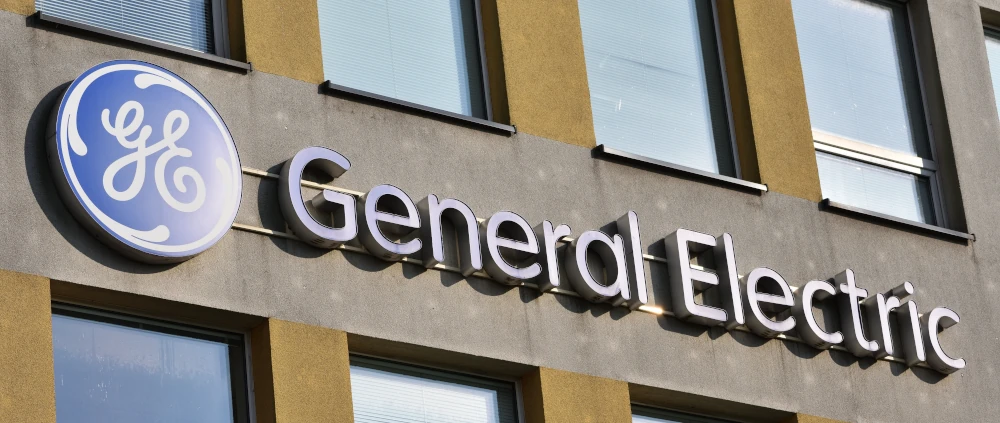
What is the Methodology for Value Engineering?
The value engineering process follows several key steps:
Information Gathering: Define the project’s goals and requirements. Collect data on costs, specifications, schedules, and engineering expectations for each design element. Analyze the existing design to understand its functions and identify potential areas for improvement.
Function Analysis: Decompose each design element into its core functions and assess their necessity for the overall project. Identify opportunities to simplify or combine functions.
Creative Brainstorming: Facilitate collaboration among team members to generate innovative alternatives. Explore options for materials, construction methods, and design approaches to identify potential cost-saving solutions.
Evaluation and Selection: Analyze alternatives based on cost, functionality, quality, and schedule impact. Obtain reliable cost data and conduct feasibility assessments to identify risks.
Development and Implementation: Finalize the selected solutions into detailed specifications, ensuring clear communication with all stakeholders. Monitor implementation to confirm cost savings while maintaining quality.
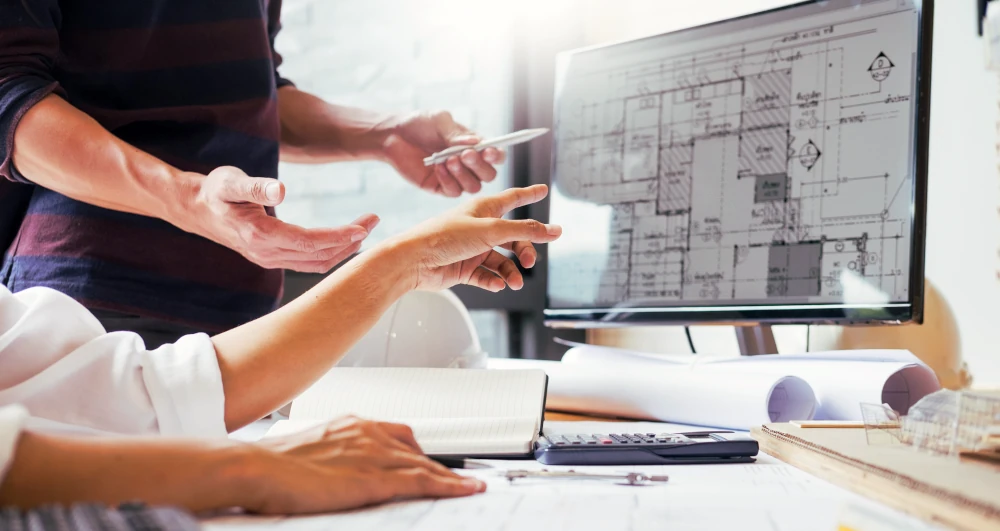
How Can 3D Laser Scanning Aid the Value Engineering Process?
Incorporating 3D laser scanning into the planning and design phases significantly enhances value engineering outcomes. By capturing precise data of existing conditions, laser scanning enables engineers, architects, and designers to optimize designs, reduce costs, and improve overall project value.
What is 3D Laser Scanning?
3D laser scanning uses advanced technology to capture high-resolution spatial data by emitting laser beams to measure distances to surfaces. The result is a point cloud that can be converted into 2D CAD drawings or 3D BIM models, enabling accurate visualization, analysis, and optimization of designs.
How Can 3D Laser Scanning Support Value Engineering?
Accurate As-Built Documentation: 3D laser scanning eliminates the need for manual measurements, reducing errors and providing a clear understanding of existing conditions. This enables precise modifications and improves the accuracy of design changes.
Clash Detection: Detailed 3D models highlight potential clashes between building components early in the design process, preventing costly rework during construction. For example, a wastewater treatment plant used an LOD 300 BIM model to optimize heat exchanger system updates.
Optimized Design Modifications: Data from laser scans and 3D models allows engineers to evaluate material substitutions or reductions without compromising structural integrity, ensuring cost-effective modifications.
Improved Material Estimation: By capturing precise measurements, 3D laser scanning reduces waste and ensures materials are cut, fabricated, and installed accurately, minimizing excess. For instance, an airport project used laser scanning to ensure prefabricated ceiling components fit perfectly, reducing on-site adjustments.
Enhanced Collaboration: A shared 3D model facilitates collaboration among teams, contractors, and stakeholders, enabling informed decision-making and cost-saving solutions. In a hotel renovation, a 2D floor plan was provided via SiteMap® for seamless communication among project teams.
Site Analysis and Feasibility Assessment: Accurate scans of existing conditions help identify potential constraints early, allowing for adjustments that optimize project feasibility.
Retrofitting and Renovation Planning: For existing buildings, laser scans provide detailed data for efficient planning, enabling minimal disruption during retrofits or renovations. Laser scanning during a retrofit project provides immediate insights for design modifications that reduce costs and downtime.
3D Laser Scanning Supports Every Stage of a Building's Lifecycle
3D laser scanning enhances the entire lifecycle of a building, from design to renovation. Its speed and accuracy allow teams to gather data quickly, reducing delays and ensuring faster decision-making. The digital record generated through scanning can be revisited for future maintenance or upgrades, adding value throughout the building's life.
Why Use Existing Conditions 3D Laser Scanning Services?
Existing Conditions 3D laser scanning offers fast, accurate, and reliable data, providing precise measurements of sites that traditional methods cannot match. Our 3D laser scanning services deliver 2-4mm accuracy with up to 2 million data points per second, enabling efficient planning, design, and construction. Our Process Team can export data to create accurate existing conditions as-builts—both above and below ground—to keep projects on schedule, within budget, and compliant.
Existing Conditions 3D Laser Scanning Services
Over the past 27 years, we have measured, documented, and modeled over 10,000 buildings spanning over 700 million square feet across the United States, establishing ourselves as an industry leader in 3D laser scanning. Architects, builders, engineers, developers, facility managers, trust us to deliver digital representations of the as-built environment with unparalleled accuracy and efficiency. Our dedicated Project Managers provide fast and accurate 3D laser scanning services and drone imagery services, and expert CAD and BIM technicians create custom, detailed deliverables. Our greatest reward remains delivering superior-quality scan-to-BIM work and knowing we played a vital role in our clients’ unique and historic projects.
FAQs
How Accurate is the Point Cloud and BIM Model?
Point clouds are a digital representation of spatial information, stored as a collection of points with three spatial coordinates. They are millimeter-accurate and are scanned in the level of detail required for your project. BIM model features are created to your project-specific scope, LOD specifications can vary throughout the model. By specifying scope and project details, BIM models can be customized to your project.
How Does Laser Scanning Work?
One primary method is that a laser scanner sends light pulses at high speeds which reflect off objects and return to the scanners’ sensor. For each pulse, the distance between the scanner and object is measured by determining the elapsed time between the sent and received pulses. Each point of the scan will be converted to a pixel with a known x-, y-, and z- coordinate. Laser scans or LiDAR scans are taken in multiple positions around a site from varying viewpoints. Millions of data points are captured and processed into a point cloud, creating an accurate data set of the structure or site.
How is CAD different from BIM?
CAD is technology and software designed to produce precise technical drawings —replacing manual hand-drawn and drafting techniques with a digital process. CAD is used in many fields, including architecture and engineering, to create accurate and efficient representations of sites.
BIM, or Building Information Modeling, is a process of visualizing a digital representation of a physical asset via the 3D model and includes richer levels of data, including information on materials and equipment. Architects, engineers, and construction managers can track and monitor a building through its entire lifecycle, from initial design to construction, operations, and maintenance. Project teams can collaborate, share information, and monitor project costs using BIM.