New York Life Building 51 Madison Avenue
Highlights
Client
Services
Categories
Equipment
The iconic 1928-built New York Life Building at 51 Madison Avenue required as-built documentation for an MEP/FP system upgrade.
The project was initiated by the building owner and managed by Gardiner & Theobald, a New York-based consultancy.
Existing Conditions used 3D laser scanning to capture precise conditions for four levels of the building's MEP/FP systems.
The deliverables included point cloud data, 2D CAD drawings, and a 3D BIM model for in-depth visualization and analysis.
These accurate data sets enabled Gardiner & Theobald to make informed decisions and reduced the risk associated with outdated documentation.
With accurate, real-time data obtained through 3D laser scanning, the project team was able to collaborate more effectively, share critical information, and coordinate with on-site trades.
Accurate data ensured that the MEP systems aligned with the building's overall design while meeting safety standards, quality requirements, and code compliance.
By relying on precise data, the team ensured that the upgraded MEP systems were safely installed, functioned properly, and provided reliable performance for the building’s future.
Case Study: New York Life Building, 51 Madison Avenue
The New York Life Building's aging MEP systems were inefficient, outdated, and posed potential safety risks. Gardiner & Theobald was contracted to plan a mechanical, electrical, plumbing (MEP), and fire protection (FP) system upgrade to modernize the aging infrastructure. Upgrading these systems was essential to improving operational efficiency, enhancing safety standards, and ensuring compliance with modern building regulations.
Gardiner & Theobald requested 3D laser scanning to accurately document The New York Life Building's structural and MEP systems before the upgrade. This technology provided a precise, high-resolution digital representation of existing conditions, allowing engineers and designers to plan efficiently, identify potential conflicts, and minimize unforeseen issues during construction.
By capturing millions of data points, the 3D laser scan ensured that modifications could be made with accuracy, reducing costly change orders, improving coordination among project teams, and preserving the building’s historic integrity while integrating modern systems.
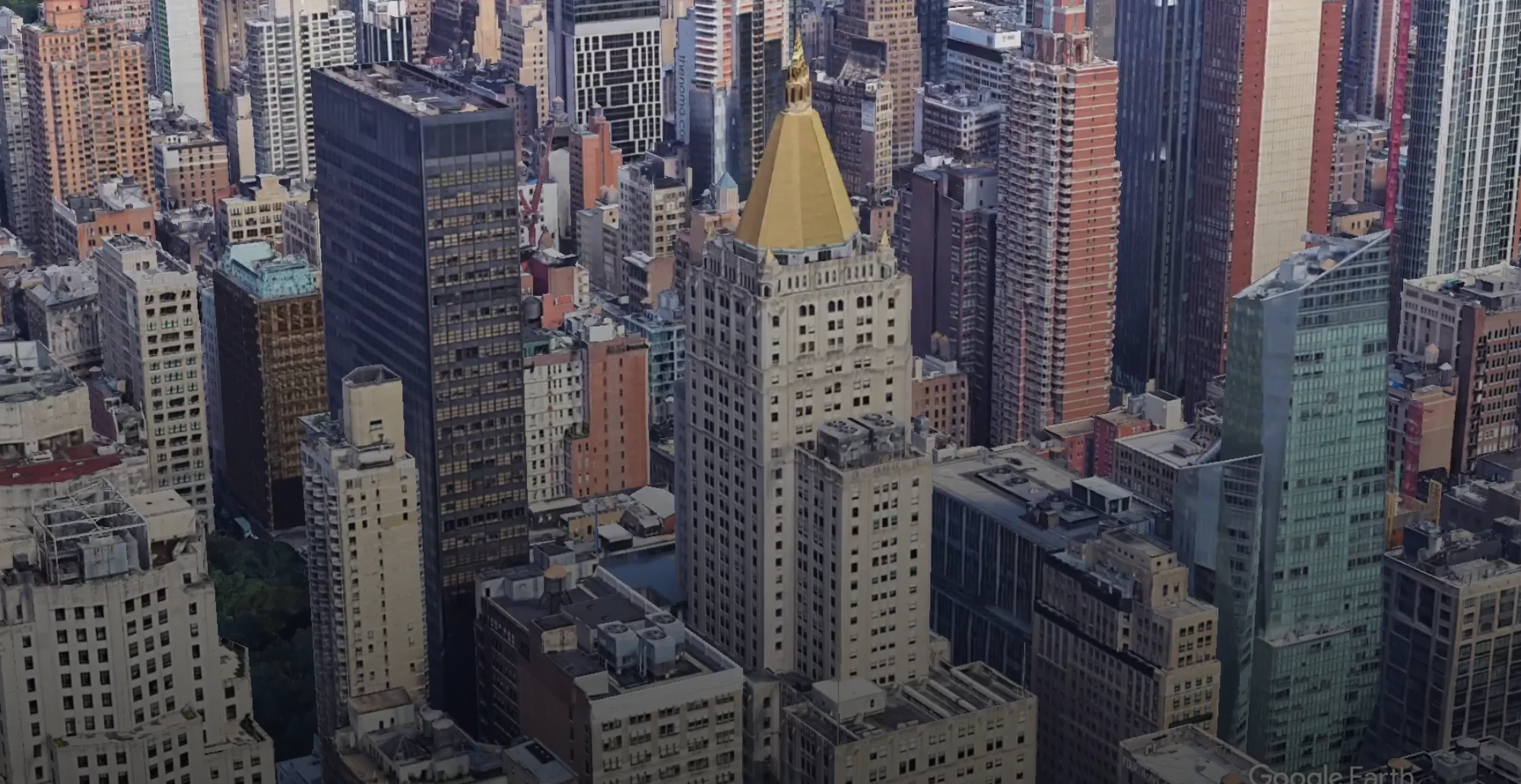
Scope of Work
The Existing Conditions team was tasked with providing precise as-built documentation for the building's four underground levels, including the basement, sub-basement, and sub-sub-basement. Each level had critical updates that were being planned but lacked accurate documentation of the existing conditions.
Existing Conditions 3D laser scanned exposed MEP and structural components to capture accurate data. Using the scan data, a detailed 3D BIM model and 2D CAD drawings were delivered to Gardiner & Theobald, enabling comprehensive visualization of the 4 levels of the building. Additionally, leveraging our expertise in similar projects, we assisted in the creation of the RFP for the renovation, helping to define project requirements and scope effectively.
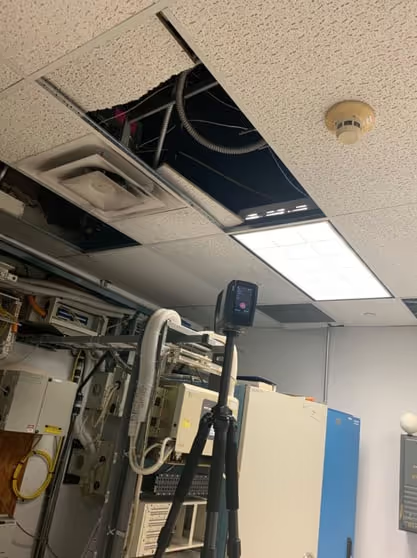
Challenge
Due to the fact that the skyscraper is, first and foremost, a center of commerce, 3D laser scanning was planned outside normal business hours to prevent disruptions to daily operations. Coordinating access, while ensuring minimal interference with tenants and staff, was a critical challenge that needed careful planning and execution.
Another major challenge was the lack of reliable as-built drawings, which increased the risk of errors potentially affecting the renovation process. Without precise records of the building’s structural and MEP systems, project teams could face potential setbacks due to unforeseen conditions.
Additionally, distinguishing active MEP systems from obsolete ones was essential for optimizing space and efficiency. Older buildings often contain abandoned infrastructure that can complicate upgrades. Identifying and mapping only the functional components ensured that the renovation focused on modernizing essential systems while removing unnecessary elements.
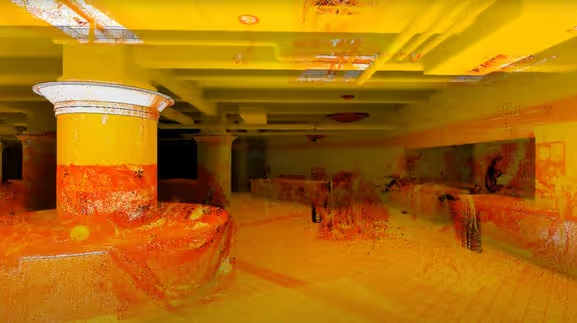
Solution
The team coordinated closely with building management to execute a minimally obtrusive fieldwork plan, ensuring comprehensive documentation of dense MEP areas while allowing normal building operations.
Using advanced 3D laser scanning technology, including Leica RTC360 and Leica BLK360 laser scanners, efficient scanning was conducted over three weeks to capture high-density, colorized 3D scan data and deliver precise documentation. The scan data provided Gardiner & Theobald’s engineers with the necessary insights to differentiate active and abandoned infrastructure, supporting optimization and retrofit planning.
The deliverables, including highly accurate 3D laser scan data, a 3D BIM model, and 2D CAD drawings, enabled the client to visualize the structure in 3D and 4D, facilitating informed decision-making, minimizing risks of costly change orders, and streamlining project planning. To ensure smooth data integration, training sessions were provided to the client's team, enabling efficient data utilization and distribution.
The MEP/FP upgrade at the New York Life Building required a highly coordinated effort to integrate modern systems into the building's existing structure. With accurate, real-time data obtained through 3D laser scanning, the project team was able to collaborate more effectively, share critical information, and coordinate with on-site trades. This seamless integration ensured that the MEP systems aligned with the building's overall design while meeting safety standards, quality requirements, and code compliance. By relying on precise data, the team ensured that the upgraded MEP systems were safely installed, functioned properly, and provided reliable performance for the building’s future.
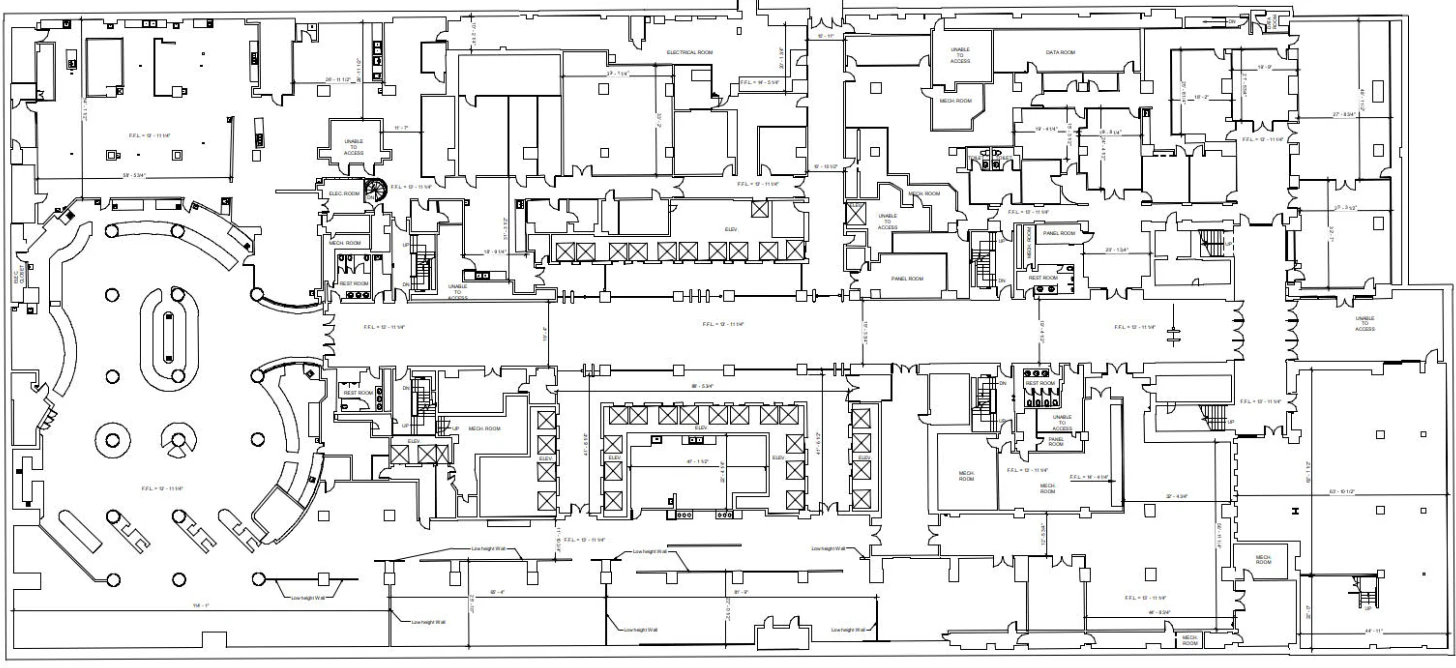
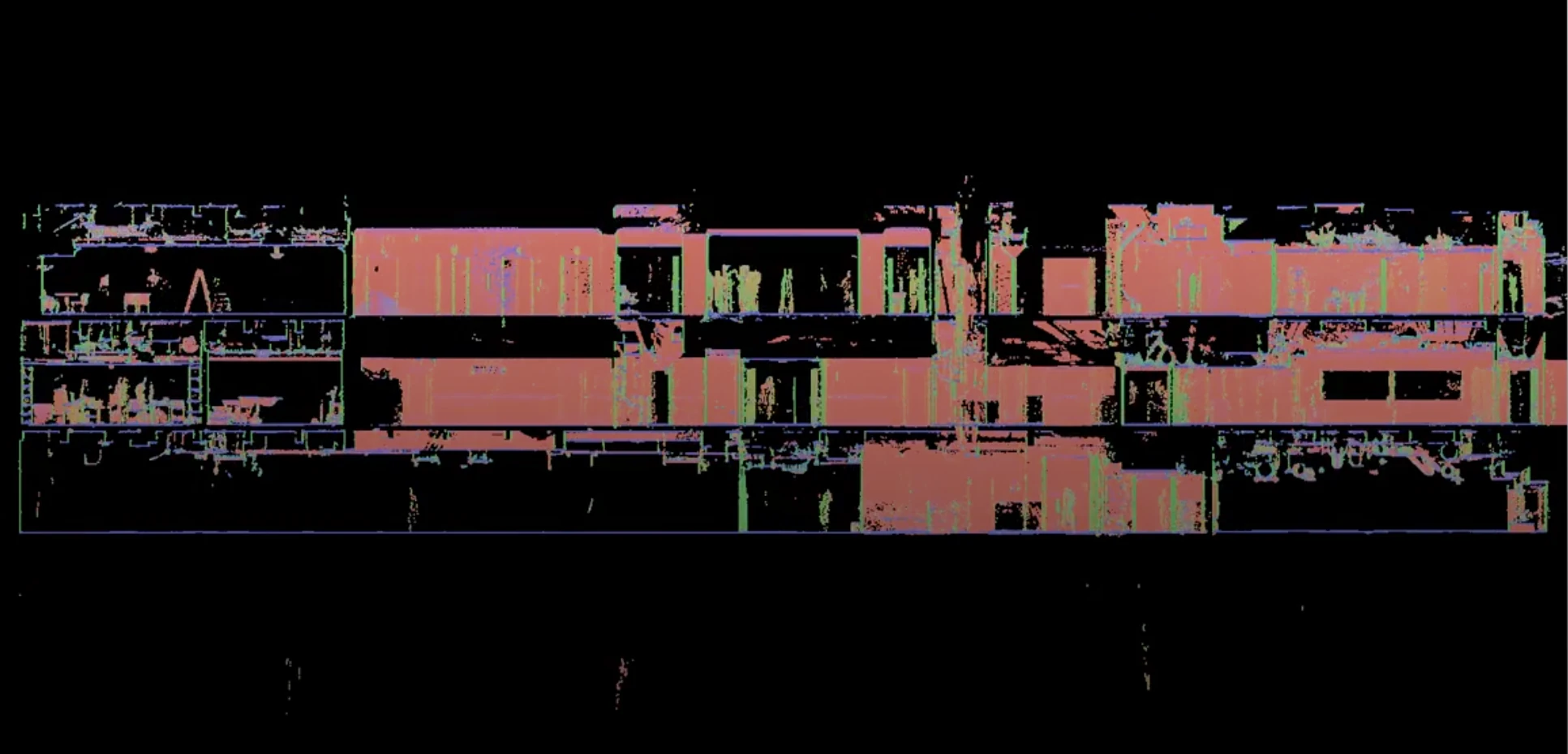
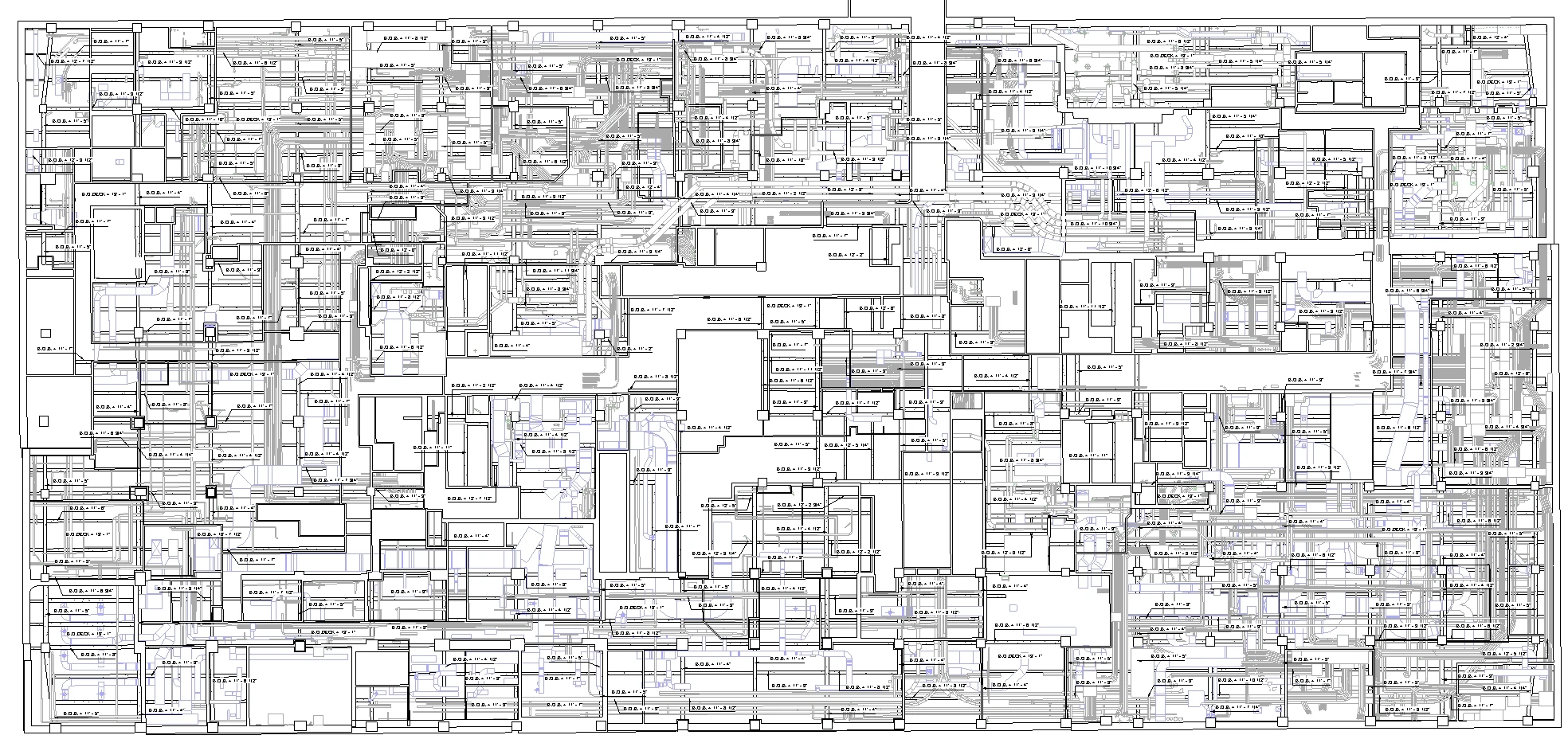
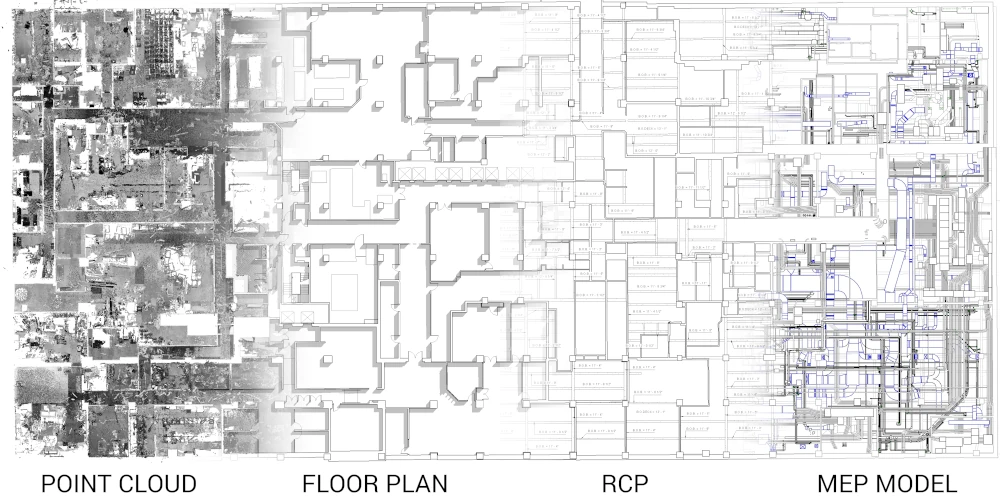
Watch the Video
Want to learn more about our partnership with Gardiner & Theobald to 3D laser scan The New York Life Building 51 Madison Avenue?
Click here to watch our case study video.
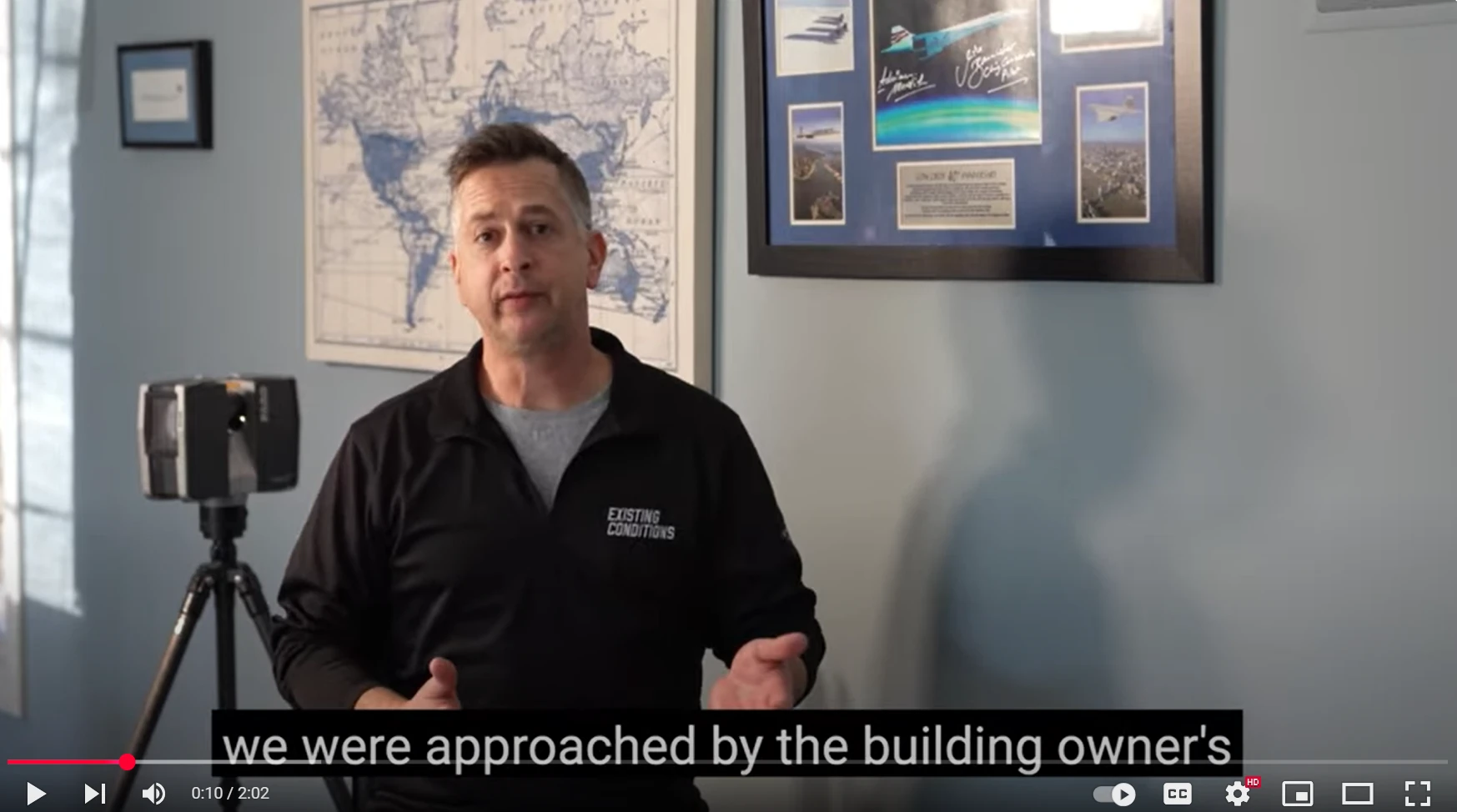
History of the New York Life Building
Completed in 1928, the New York Life Building stands as a masterpiece of neo-Gothic architecture. It was designed by renowned architect Cass Gilbert and constructed between 1926 and 1928 as the new headquarters for the New York Life Insurance Company. The building stands 40 stories and sits prominently at 51 Madison Avenue, on the northern edge of Madison Square Park. With its intricate Gothic details and limestone façade, the building’s design reflects the grandeur and ambition of the early 20th century. The crowning glory of the New York Life Building is its gilded roof, made up of over 25,000 individual gold-leafed terracotta tiles. In 1978, the building was designated a National Historic Landmark and in 2000 as a New York City Historic Landmark.
About the Client: Gardiner & Theobald
Gardiner & Theobald is an independent global consultancy specializing in project, cost, and management for the construction and property industry. The company focuses on minimizing risk and creating opportunities to maximize the value of their clients’ developments and property assets.
Gardiner & Theobald Inc. has been operating across North America for 24 years, delivering diverse projects for a blue-chip client portfolio that includes occupiers, developers, contractors, financial institutions, and local and central governments.
Their projects span the breadth of the built environment, including but not limited to landscaping and master planning, luxury hospitality, high-end residential, commercial developments, civic buildings, and museums.
Existing Conditions has previously collaborated with Gardiner & Theobald on projects such as 140 Broadway in Brooklyn, New York and The New York Stock Exchange in New York, New York.
Existing Conditions 3D Laser Scanning Services
Over the past 27 years, Existing Conditions has measured, documented, and modeled over 10,000 buildings across the United States, establishing ourselves as an industry leader in 3D laser scanning.
Architects trust us to deliver digital representations of the as-built environment with unparalleled accuracy and efficiency. Our dedicated Project Managers provide fast and accurate 3D laser scanning services and drone imagery services, and expert CAD and BIM technicians create custom, detailed deliverables, including point clouds, 2D CAD drawings, 3D BIM models, 3D mesh models, TruViews, and 3D virtual tours.
Our greatest reward remains delivering superior-quality scan-to-BIM work and knowing we played a vital role in our clients’ historical architecture and preservation projects.
Contact us today for a free project estimate.
Related Case Studies
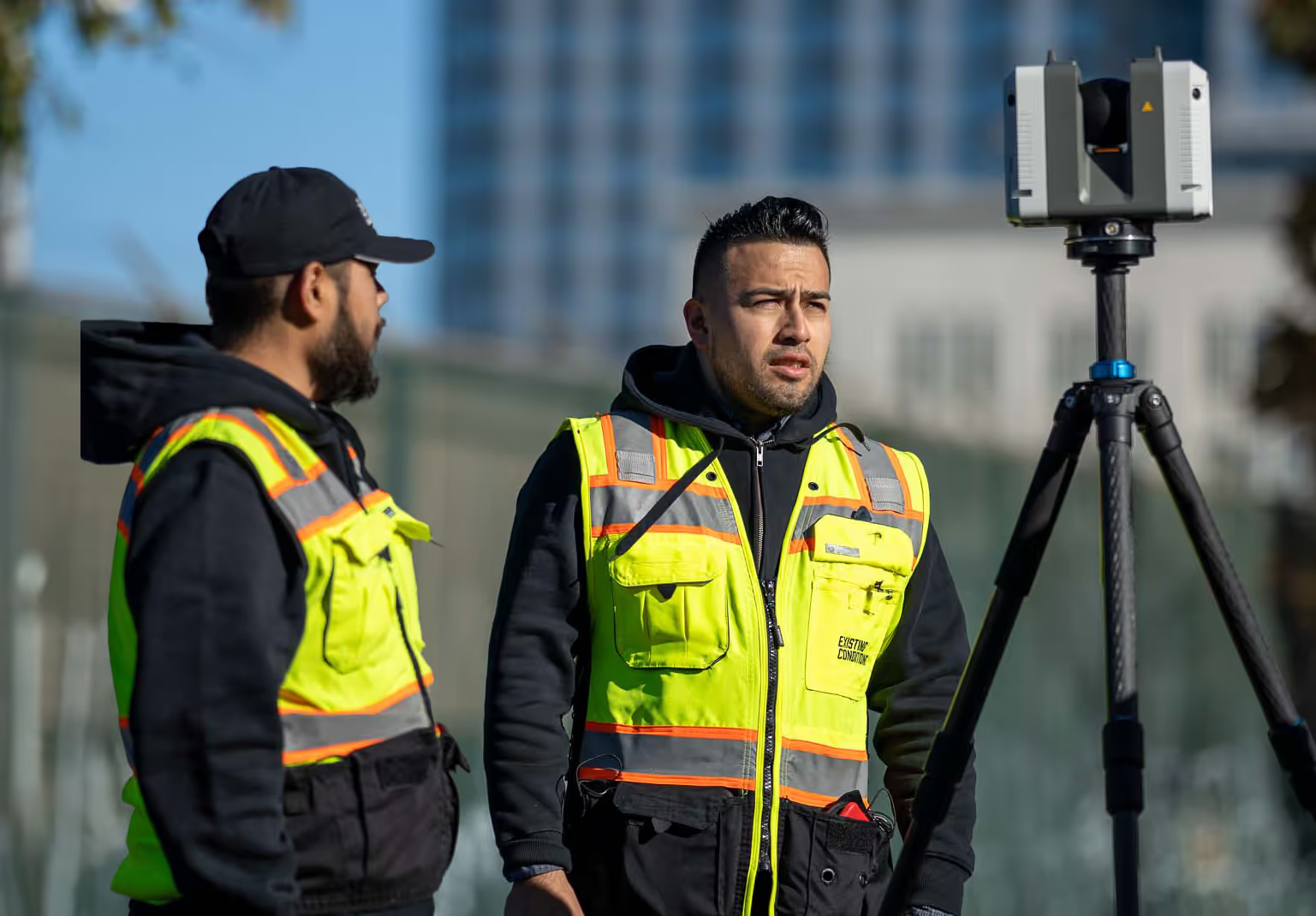