Is a “Kit of Parts” the Future of Commercial Construction?
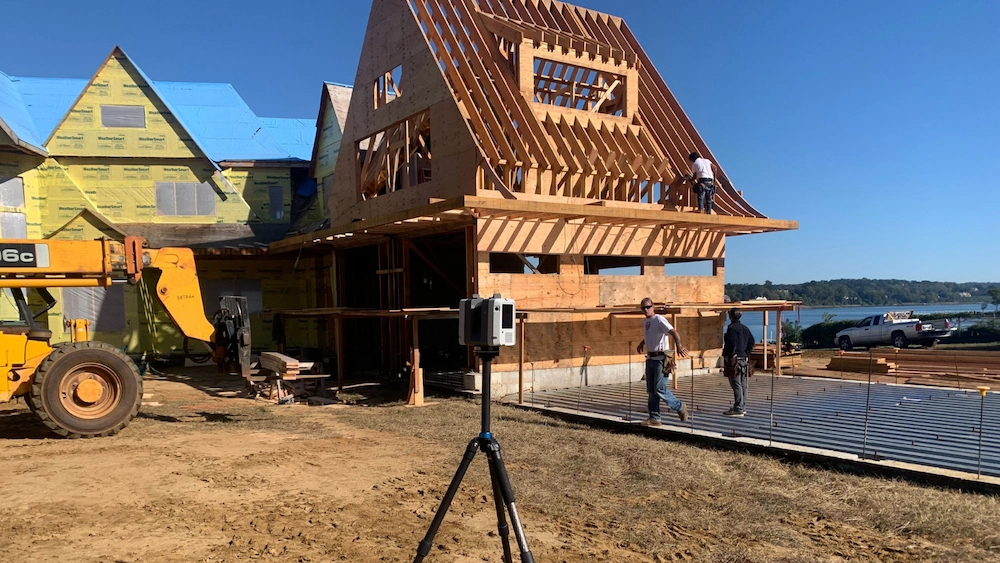
Imagine a world where buildings come together like LEGO sets: pre-designed, precision-manufactured, and assembled on-site with minimal waste and maximum efficiency. This is the essence of the "Kit of Parts" approach, a method rapidly reshaping the building industry.
For architects, engineers, and developers, this approach offers faster, more cost-effective, and sustainable ways to bring designs to life. At Existing Conditions, we’re helping drive this transformation by providing accurate as-built documentation for existing buildings – for example, assisting teams to detect and avoid clashes before fabrication, reducing costly rework, delays, and material waste.
By partnering with GPRS, we can help you expand that precision even further. When you combine above-ground reality capture with underground utility locating and mapping, you can provide your construction and design teams with the most comprehensive site intelligence possible. The result? A streamlined, data-driven approach that ensures every component integrates effortlessly.
But how does this modular strategy work? And why are leading firms embracing it as the future of commercial construction?
What is a “Kit of Parts” Approach to Construction?
The Kit of Parts method is a construction approach that relies on standardized, prefabricated components that are manufactured off-site and then assembled on location.
Instead of traditional stick-built construction, where every part is cut, shaped, and built on-site, this method treats buildings like puzzle pieces – each designed for easy assembly while still allowing for customization.
Why is This Approach Gaining Traction?
Construction projects are becoming larger, more complex, and more expensive. Companies are under increasing pressure to build faster, reduce costs, and improve sustainability. The Kit of Parts method addresses these challenges head-on by offering:
Faster Project Timelines: Prefabricated components are built in controlled environments, eliminating weather-related delays and reducing site-based inefficiencies. By ensuring accurate fits before installation, teams can avoid last-minute adjustments, schedule disruptions, and costly rework, keeping projects on track.
Cost Savings: Prefabrication significantly reduces material waste, minimizes on-site labor hours, and lowers the risk of errors that lead to expensive rework. With fewer clashes and adjustments needed during installation, teams can stay on budget and avoid unexpected costs.
Improved Quality Control: Standardized production ensures a higher level of accuracy, reducing construction defects that often result in time-consuming corrections. With precise as-built documentation and clash detection, teams can catch issues before they escalate, preventing delays and unnecessary expenses.
Greater Sustainability: Prefabrication minimizes construction waste, leading to a smaller environmental footprint and more efficient material use. With fewer on-site deliveries and a reduced need for rework, projects see lower carbon emissions and a more streamlined construction process.
Flexibility for Future Expansions: A modular approach using a Kit of Parts allows for easier reconfiguration and expansion over time. Standardized components fit seamlessly into existing structures, reducing the need for major redesigns and costly adjustments during future modifications.
From multifamily housing to commercial offices and industrial facilities, this approach is being embraced across industries looking to streamline operations and improve project efficiency. But to make it work, teams need accurate data, this is where Existing Conditions and GPRS step in.
How Does Existing Conditions Support the Kit of Parts Method?
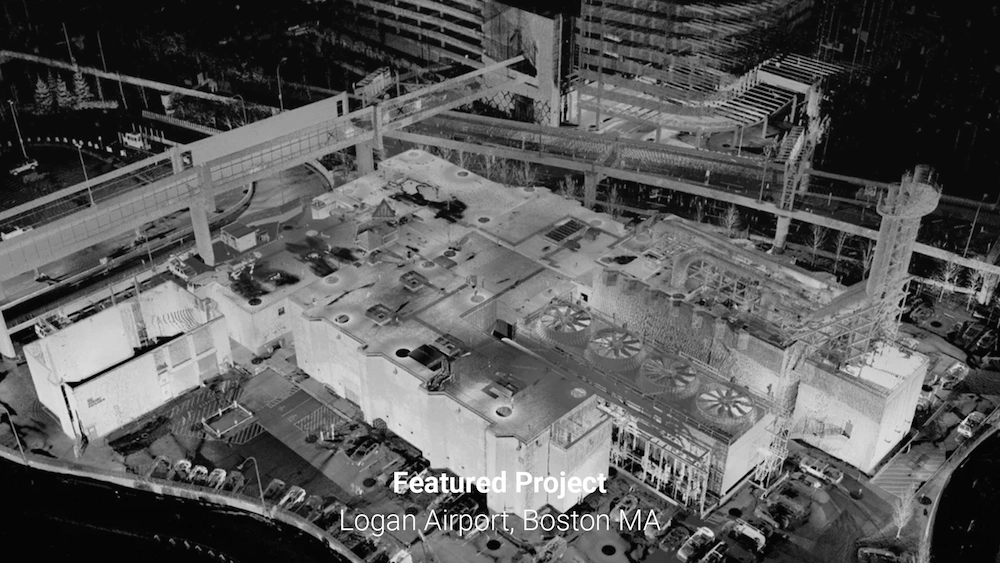
The success of any Kit of Parts project depends on accurate data, and that's exactly what Existing Conditions’ delivers. Before any modular components are built, we ensure that architects, engineers, and contractors have a 100% accurate understanding of the existing site and structures.
Our Role in Making Modular Construction Possible
3D Laser Scanning: We capture existing conditions with high accuracy, creating a precise digital representation of the building or structure. This level of detail reduces guesswork, minimizes costly rework, and allows teams to confidently plan modifications – ensuring better coordination and fewer onsite surprises.
Reality Capture and BIM Modeling: We transform laser scan data into detailed Revit models, point clouds, and CAD drawings, allowing for seamless integration of prefabricated components. This level of accuracy helps reduce rework and accelerates project timelines by ensuring all elements fit as intended before they reach the site.
As-Built Documentation: Our accurate architectural drawings provide a reliable foundation for architects, engineers, and contractors to design and execute modular components with confidence. By working from precise, up-to-date documentation, teams can avoid costly delays and enhance collaboration
.
Modular construction requires this level of precision to be successful. Imagine if a prefabricated floor slab arrived on-site only slightly too big or small. A mistake that could lead to costly delays, redesigns, and wasted materials.
By integrating 3D laser scanning, modeling, and digital documentation into the planning process, we help construction and design teams avoid these pitfalls, ensuring that every part of a Kit of Parts project is built for success.
How GPRS Enhances the Kit of Parts Approach
Now that Existing Conditions is part of GPRS, we’re bringing a more powerful suite of services to the table. While we specialize in above-ground reality capture, GPRS focuses on subsurface scanning, concrete scanning and imaging, video pipe inspection, leak detection, and utility locating and mapping. By integrating some or all these tools and technologies, you can get a complete picture of the built environment, above-ground and below, before construction begins.
With SiteMap®, GPRS’ proprietary project management platform, you can visualize and collaborate on these datasets in one centralized location. SiteMap® provides an interactive, cloud-based interface where teams can access and analyze reality capture data, subsurface mapping, and as-built documentation in real-time. This ensures that stakeholders across architecture, engineering, and construction have the critical insights to prevent clashes, streamline decision-making, and keep projects on schedule.
How Our Combined Expertise Helps ModularConstruction Projects
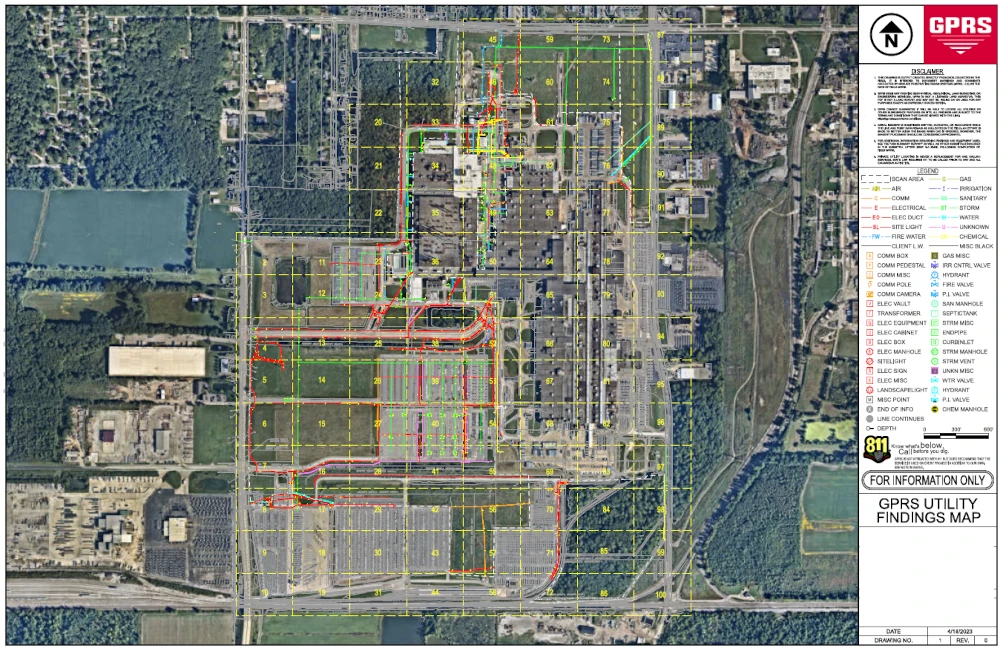
Utility Locating and Concrete Scanning: GPRS utilizes complementary technologies like ground penetrating radar(GPR) and electromagnetic(EM) locating, to help construction teams avoid costly surprises by identifying and mapping underground utilities, post tension cables, rebar, and conduit in concrete slabs, and finding other hidden obstacles.
3D Laser Scanning and BIM Modeling: Existing Conditions as-built documentation reduces the risk of prefabricated components misaligning with existing structures. By capturing highly accurate 3D laser scan data, we help ensure seamless integration between design and reality.
Seamless Integration for Smarter Construction: Our comprehensive site data equips architects, engineers, and contractors with the insights they need to make informed decisions from day one. By eliminating uncertainties, we help streamline project planning, reduce rework, and improve overall efficiency.
This integrated approach to above and below-ground site visualization allows a Kit of Parts construction project to be faster, safer, and more predictable than ever before. Helping teams stay on schedule, reduce risk, and optimize costs by providing accurate, real-time data for better decision-making.
Why the Kit of Parts Approach May Be the Future ofConstruction
As labor shortages, supply chain disruptions, and rising material costs continue to challenge the construction industry. The demand for more efficient, scalable, and cost-effective building methods is only increasing.
Key Factors Driving Adoption
Growing Demand for Speed: Developers are under pressure to deliver projects faster than ever, making prefabrication an attractive solution, for improving efficiency and reducing timelines.
Urban Density and Site Constraints: In crowded cities, traditional construction can be slow and inefficient. Kit of Parts construction allows buildings to be assembled quickly with minimal disruption.
Sustainability Goals: With a stronger emphasis on carbon reduction and waste minimization, prefabrication aligns with industry-wide efforts to build greener.
Technology-Driven Design: Advancements in 3D laser scanning, BIM modeling, and digital construction planning make it easier than ever to implement modular strategies with fewer clashes and change orders.
At Existing Conditions, we’re at the forefront of this transformation. Helping clients harness the power of accurate data, digital documentation, and advanced site intelligence to make Kit of Parts construction a reality.
Building Smarter, Faster, and More Accurately with Existing Conditions and GPRS
The future of construction isn’t about building, it’s about building smarter. The Kit of Parts approach represents a shift toward data-driven, precision-engineered construction. Where every piece fits and projects run seamlessly from start to finish.
By combining the expertise of Existing Conditions and GPRS, we provide unmatched accuracy, risk reduction, and efficiency. Helping architects, engineers, and contractors bring modular, prefabricated projects to life with confidence.
Ready to visualize your next project?
Connect with us today to learn how our advanced 3D laser scanning, as-built documentation, and utility mapping services can support your Kit of Parts project.
FAQs
How Does Laser Scanning Work?
One primary method is that a laser scanner sends light pulses at high speeds which reflect off objects and return to the scanners’ sensor. For each pulse, the distance between the scanner and object is measured by determining the elapsed time between the sent and received pulses. Each point of the scan will be converted to a pixel with a known x-, y-, and z- coordinate. Laser scans or LiDAR scans are taken in multiple positions around a site from varying viewpoints. Millions of data points are captured and processed into a point cloud, creating an accurate data set of the structure or site.
What are the Benefits of 3D Laser Scanning?
3D laser scanning captures millions of 3D data points per second for each scan location, providing incredibly rich data of a building or project site. Sites are captured in high detail the first time, eliminating disruption and the need for return visits. Datasets are dimensionally accurate, measurable and shareable, expediting project planning and execution. Accurate design plans are produced from the start expediting field work and reducing change orders, delays and costs. Communication is improved, teams can discuss plans while each has access to the same information, creating a more dynamic working environment.
How can Existing Conditions support my project's success?
By choosing Existing Conditions as your as-built survey company, you're partnering with a team of experienced professionals. Understanding building language is important when working with architects, builders, engineers, and facility managers. We have professionals trained by architects and commercial real estate investors on our staff, so we can speak the language and deliver what is needed to advance the project. Our track record speaks for itself, partnering with top professionals in the building industry, including Gensler, Studio Troika, Shawmut Construction, the New York Stock Exchange, Williams College, and Harvard University.