10 Essential Applications for 3D Laser Scanning
.avif)
Applications for 3D Laser Scanning
3D laser scanning has become a vital tool for architects and other AEC professionals due to its accuracy, speed, and adaptability. By integrating this 3D technology at the outset of a project, teams can collect precise data, as-built drawings and 3D BIM models, reducing design conflicts and expediting planning, prefabrication, asset management, and facility modifications. Below are ten key applications for 3D laser scanning.
1. Building Renovations
3D laser scanning provides detailed as-built documentation of a building’s current state, capturing architectural, structural, and MEP features such as walls, windows, doors, stairs, roofs, railings, columns, beams, equipment, piping, and ducts. This technology delivers point clouds that can be converted into 2D CAD drawings or 3D BIM models, ensuring that proposed renovations are aligned with the existing structure.
Overlaying proposed design elements onto scan data allows for the early identification and resolution of potential clashes. This process is essential for renovation projects involving stadiums, theaters, historic buildings, churches, and schools, providing a comprehensive as-built foundation for planning, design, and construction.
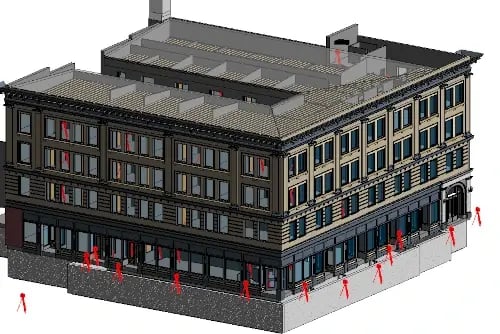
2. Architectural Design
3D laser scanning supports the architectural design process by delivering precise existing conditions to create design models, track construction progress, and verify as-built accuracy. With accuracy levels typically within 2-4mm for point clouds and 6mm for as-built models, this technology significantly enhances design precision.
Scans capture all visible structural and MEP elements, allowing architects to focus on design development rather than data collection. This streamlined approach accelerates project timelines and improves design accuracy.
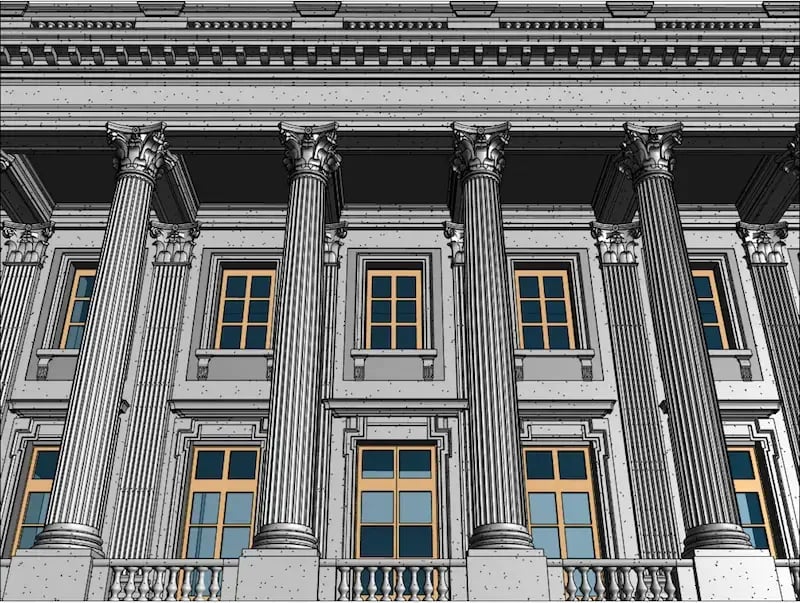
3. Power Plant Maintenance, Retrofitting, or Expansion
As power plants evolve to meet regulatory requirements or adopt new technology, modifications to existing infrastructure are often necessary. 3D laser scanning captures detailed as-built data, including structural elements, piping, boilers, turbines, pumps, condensers, and more.
This comprehensive documentation enables engineers to plan retrofits and expansions with minimal disruption. By using 2D CAD drawings and 3D BIM models derived from point clouds, engineers can design around existing infrastructure and avoid clashes. Virtual walkthroughs of scan data allow stakeholders to assess conditions remotely, reducing safety risks and enabling proactive maintenance.
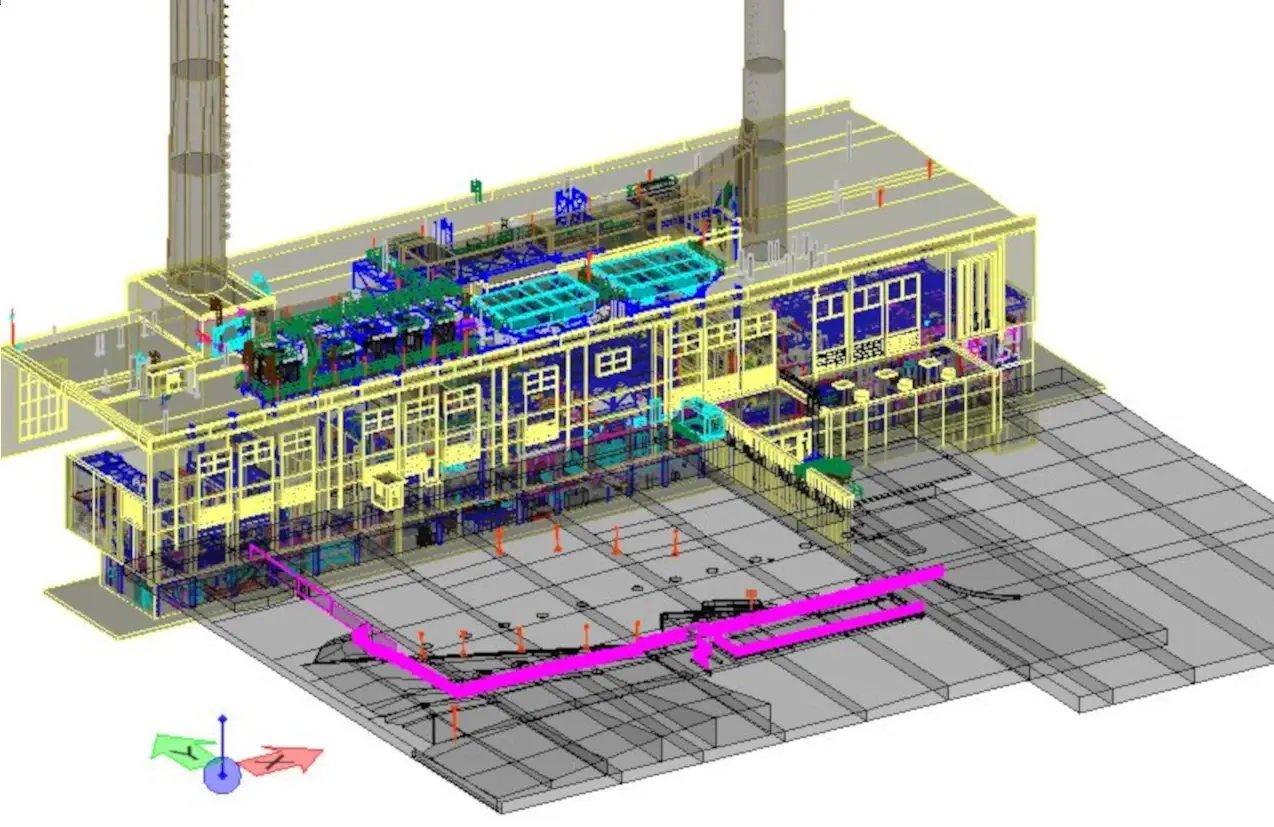
4. Manufacturing Plant Modifications, Expansions, or Maintenance
Accurate as-built data from 3D laser scanning supports the modification, expansion, or maintenance of manufacturing plants. Point cloud data is converted into 3D models for planning, fabrication, and clash detection. This ensures that machinery and process changes are accurately mapped, optimizing facility layouts and enhancing safety compliance.
Virtual fit-outs validate that new installations will integrate seamlessly with existing conditions, reducing risk, minimizing rework, and accelerating production schedules.
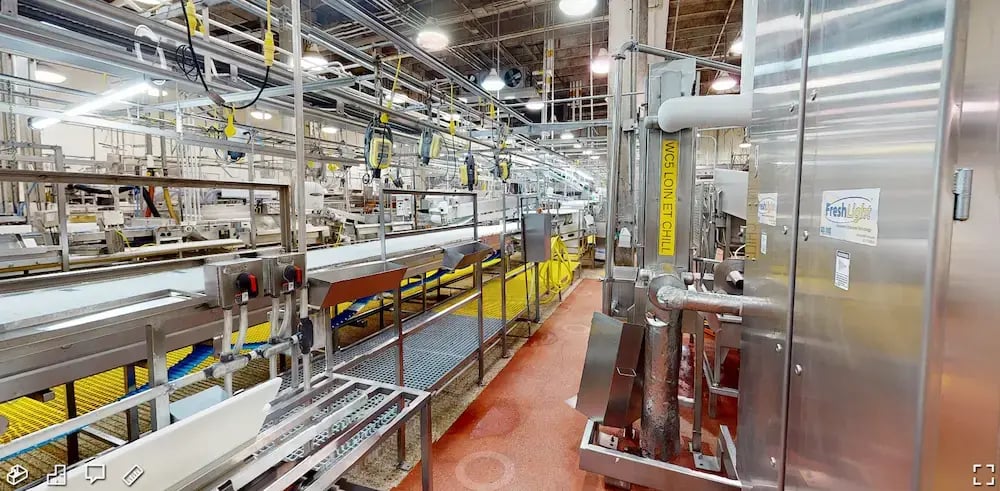
5. Floor Flatness and Levelness Measurements
3D laser scanning provides a fast and precise method for measuring floor flatness (FF) and floor levelness (FL) on concrete slabs. The resulting point cloud data is used to create color-coded elevation maps, which identify high and low points that require adjustment.
These elevation maps allow for quick and precise cut-and-fill calculations, facilitating smooth collaboration among contractors. The ability to visualize floor discrepancies ensures stakeholders remain informed, enabling timely corrections and project validation with measurable data.
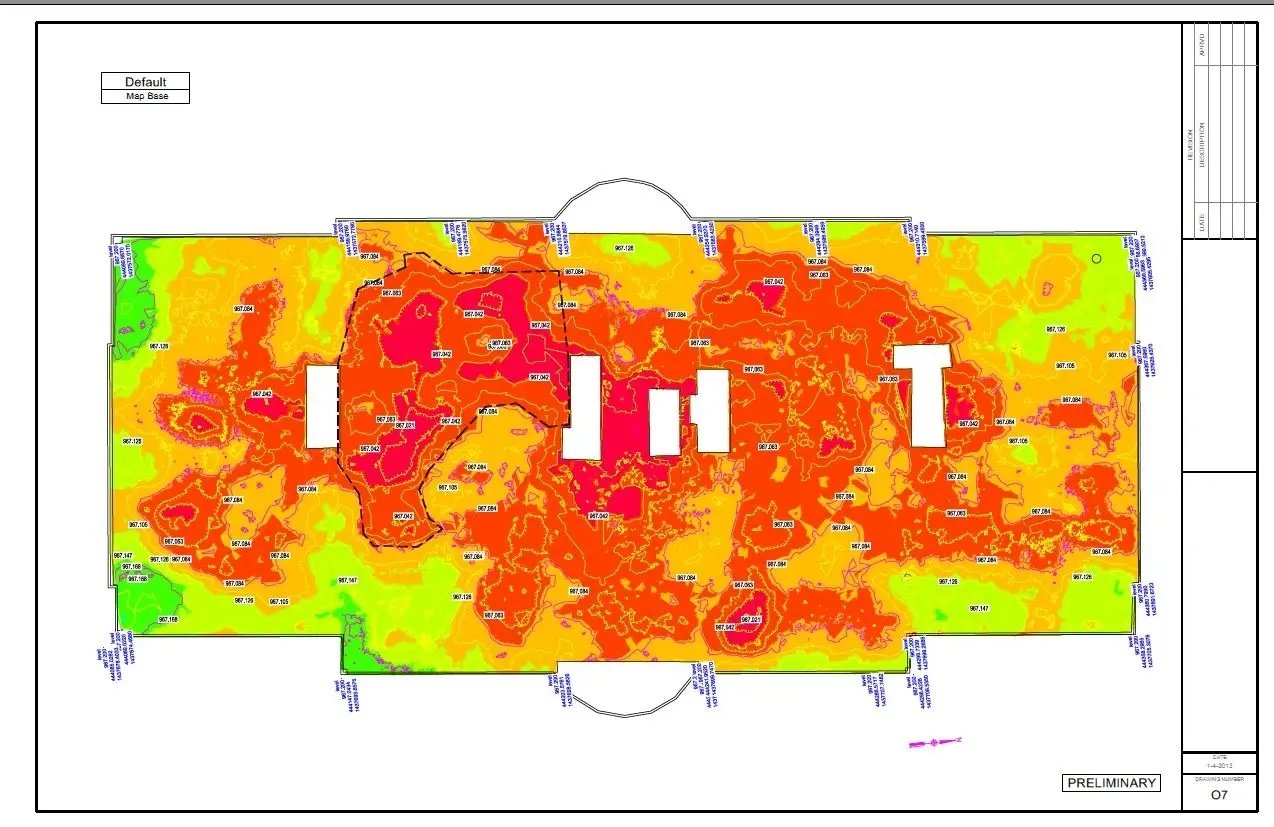
6. Creation of a Digital Twin 3D Model
A digital twin is a virtual representation of a physical space, including architectural, structural, and MEP systems. 3D laser scanning accurately captures these existing conditions to create a real-time digital model that supports design planning, facility management, and operational efficiency.
Digital twins provide a fully navigable 3D environment, enabling virtual walkthroughs for stakeholders to assess the site and plan improvements. This approach increases workflow efficiency, enhances decision-making, and supports ongoing asset management.
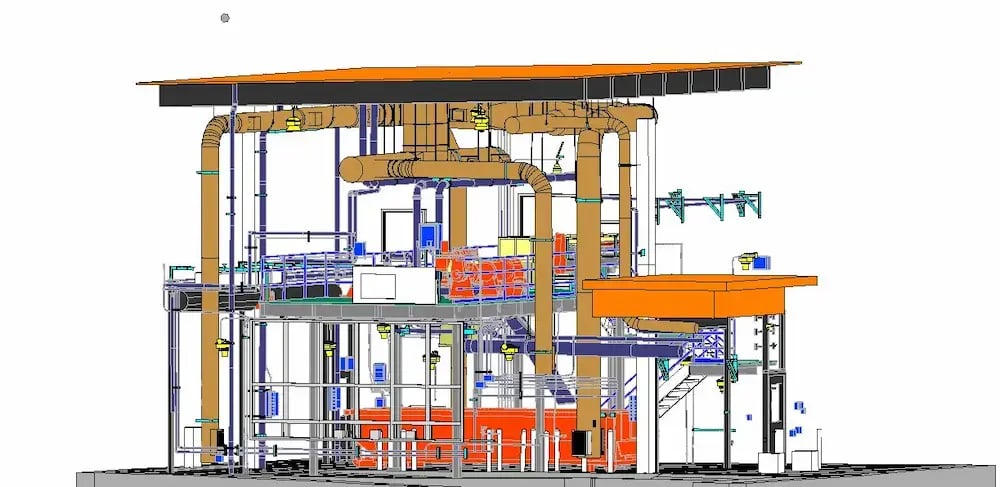
7. Retrofitting Pipes and Equipment into Existing Facilities
Accurate existing conditions are essential when retrofitting new piping, valves, or equipment into existing facilities. 3D laser scanning captures the infrastructure of facilities like water treatment plants, healthcare facilities, oil and gas refineries, and industrial plants.
With as-built data, engineers create precise 2D CAD drawings and 3D models for interference checks and clash detection. This ensures a seamless fit, reduces costly rework, and accelerates project timelines. Scan data also supports virtual pre-installation planning, further reducing the risk of project delays.
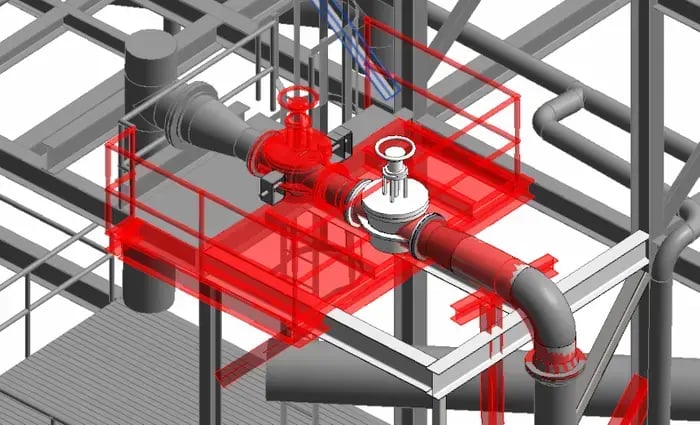
8. Creation of 2D CAD Drawings for Permit Applications
To secure building permits, comprehensive construction documents must be submitted. 3D laser scanning captures existing conditions with 2-4mm accuracy, providing the precise layout and dimensions required for site plans, floor plans, elevations, sections, and detail drawings.
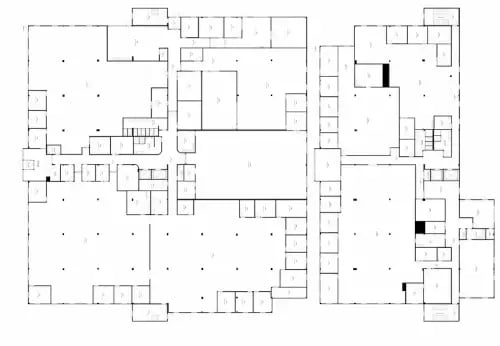
9. 3D Mesh Model Development
3D mesh models are highly detailed representations of buildings, objects, or sites. These models, often used for architectural visualization or mixed reality experiences, are created from point cloud data and exported in formats like .fbx, .stl, .obj, or .ply.
Mesh models capture intricate spatial details, such as the geometry of monuments, aircraft, cars, or sports arenas. By using mesh models, architects can visualize and communicate design concepts with unparalleled clarity and realism.
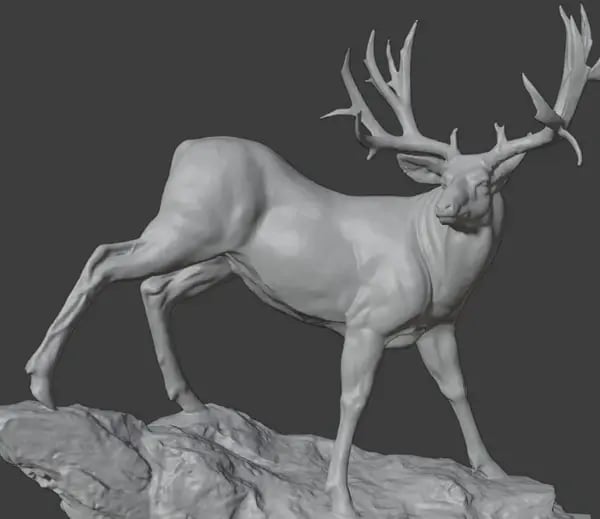
10. P&ID Updates
A piping and instrumentation diagram (P&ID) illustrates the layout of piping, vessels, valves, and control devices in a process plant. 3D laser scanning captures this as-built data with a high level of accuracy, which can be used to update P&ID drawings to reflect the current state of a facility.
Accurate documentation of existing piping, equipment, and control devices ensures the P&ID remains up to date for future reference, modifications, and maintenance. By integrating 2D CAD drawings and 3D BIM models, stakeholders gain a comprehensive view of the facility’s process systems.
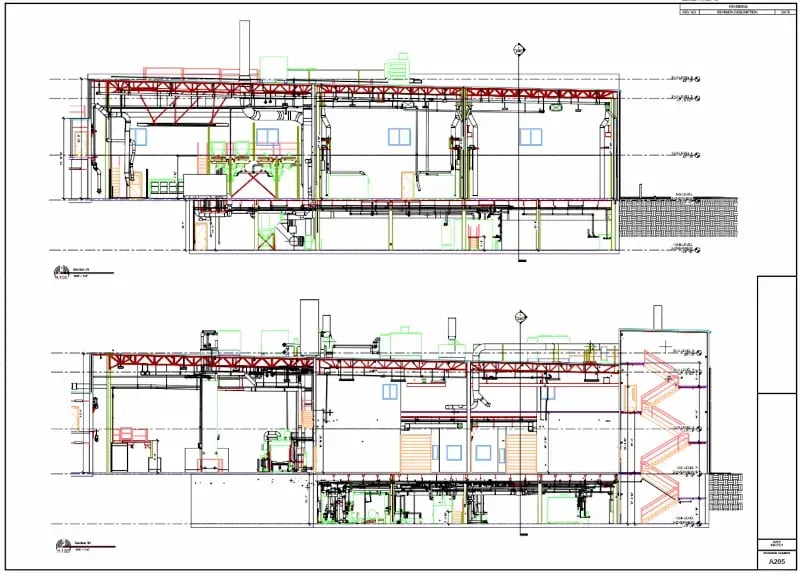
The Existing Conditions Difference: Why Choose Existing Conditions?
Accurate measurements are essential to avoid costly mistakes, rework, and change orders. Existing Conditions’ 3D laser scanning services (now a GPRS Company) provide construction-grade documentation of existing site conditions, supporting efficient planning, design, and construction.
Our expert Project Managers use advanced Leica laser scanners to capture the layout, dimensions, and locations of project-specific architectural, structural, and MEP features, such as walls, windows, doors, stairs, roofs, railings, beams, and equipment.
We also process point cloud data to remove noise and set a coordinated system for precise measurements. Custom 2D CAD drawings and 3D BIM models are delivered via SiteMap®, a cloud-based software that offers point cloud data, 2D CAD files, and 3D BIM models in a single platform.
What can we help you visualize?
Existing Conditions 3D Laser Scanning Services
Over the past 27 years, we have measured, documented, and modeled over 10,000 buildings spanning over 700 million square feet across the United States, establishing ourselves as an industry leader in 3D laser scanning. Architects, builders, engineers, developers, facility managers, trust us to deliver digital representations of the as-built environment with unparalleled accuracy and efficiency. Our dedicated Project Managers provide fast and accurate 3D laser scanning services and drone imagery services, and expert CAD and BIM technicians create custom, detailed deliverables. Our greatest reward remains delivering superior-quality scan-to-BIM work and knowing we played a vital role in our clients’ unique and historic projects.
FAQs
What are the Benefits of 3D Laser Scanning?
3D laser scanning captures millions of 3D data points per second for each scan location, providing incredibly rich data of a building or project site. Sites are captured in high detail the first time, eliminating disruption and the need for return visits. Datasets are dimensionally accurate, measurable and shareable, expediting project planning and execution. Accurate design plans are produced from the start expediting field work and reducing change orders, delays and costs. Communication is improved, teams can discuss plans while each has access to the same information, creating a more dynamic working environment.
How is CAD different from BIM?
CAD is technology and software designed to produce precise technical drawings —replacing manual hand-drawn and drafting techniques with a digital process. CAD is used in many fields, including architecture and engineering, to create accurate and efficient representations of sites.
BIM, or Building Information Modeling, is a process of visualizing a digital representation of a physical asset via the 3D model and includes richer levels of data, including information on materials and equipment. Architects, engineers, and construction managers can track and monitor a building through its entire lifecycle, from initial design to construction, operations, and maintenance. Project teams can collaborate, share information, and monitor project costs using BIM.
What is a 3D BIM Model?
A building information model (BIM) is a digital representation of the physical and functional characteristics of a building or infrastructure project. BIM stores all the information about a building's life cycle in one place, including design, construction, and operational data, which can be used for planning, renovation, and maintenance. It provides accurate spatial relationships and manufacturer details, as well as geographic information and other pertinent aspects of the building.