Riverside Labs Life Sciences Campus
Highlights
Client
Services
Categories
Equipment
Case Study: Riverside Labs
The case study on the Riverside Labs project highlights the collaboration between Existing Conditions and Shawmut Design and Construction. By providing comprehensive documentation and coordination services both pre- and post-demolition, Existing Conditions demonstrated adaptability and expertise crucial for the success of the endeavor. Read on to learn how Existing Conditions' experience and coordination facilitated the smooth progression of the Riverside Labs project, ultimately contributing to its successful transformation into a premier life sciences campus.
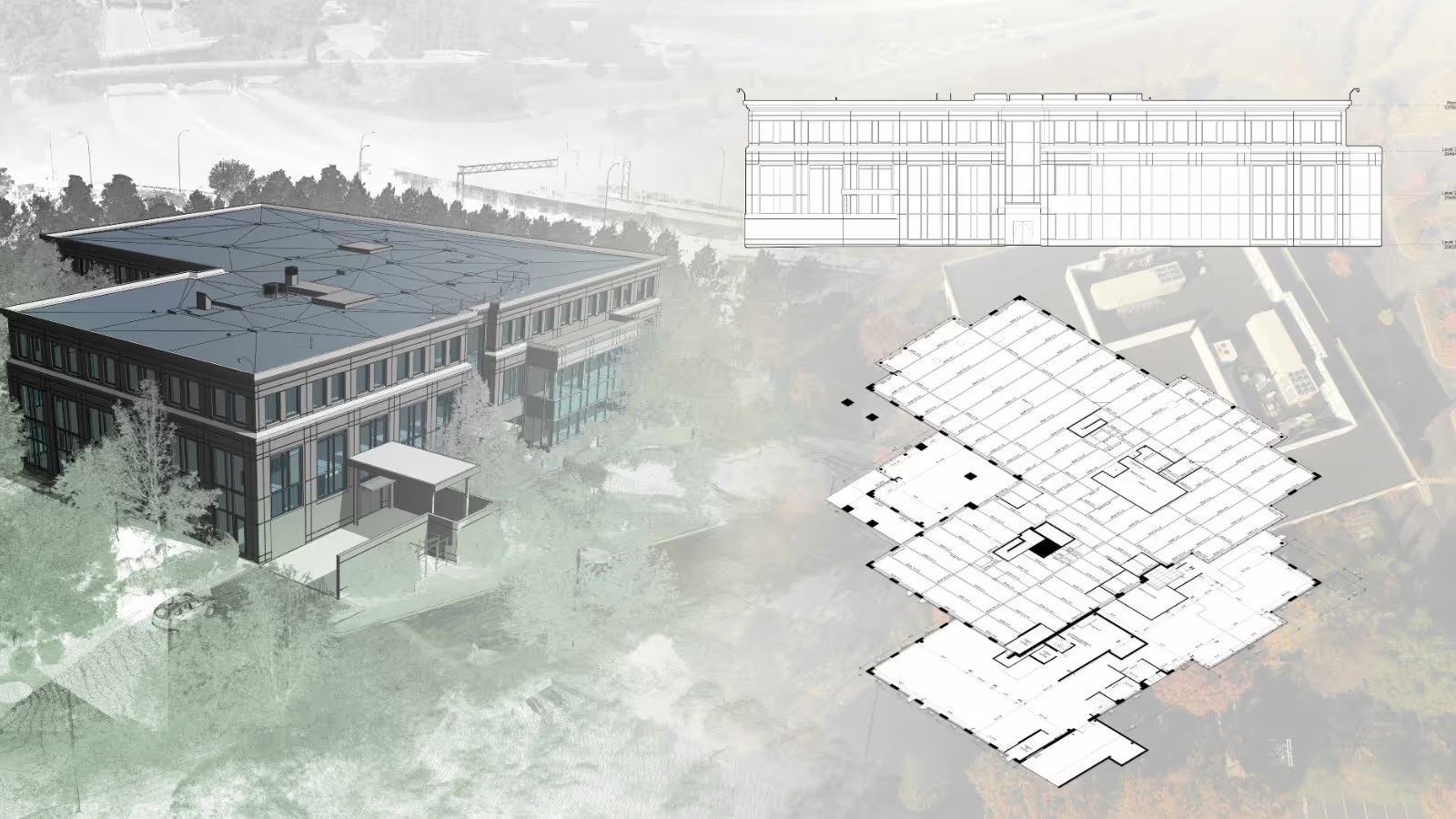
About Riverside Labs
Riverside Labs, stands as a premier life sciences campus of unparalleled distinction. Spanning 340,000 square feet on a 16-acre plot, it presents vast opportunities. Located conveniently at the crossroads of Interstates 90 and 95, it's just a short drive from both Boston and Cambridge.
Previously known as the Liberty Mutual Complex, Riverside Labs was once the headquarters of Liberty Mutual but was sold before the COVID-19 pandemic. There are three buildings at Riverside Labs: 9 Riverside, 15 Riverside, and 20 Riverside. 20 Riverside is the most recent addition and is the focus of renovation. Unlike the others, 20 Riverside is not being completely demolished but transformed from an office space into a combination of lab and office areas, with a planned split of 60% lab space and 40% office space. It is designed to accommodate multiple tenants, potentially housing two or three, depending on their space requirements.
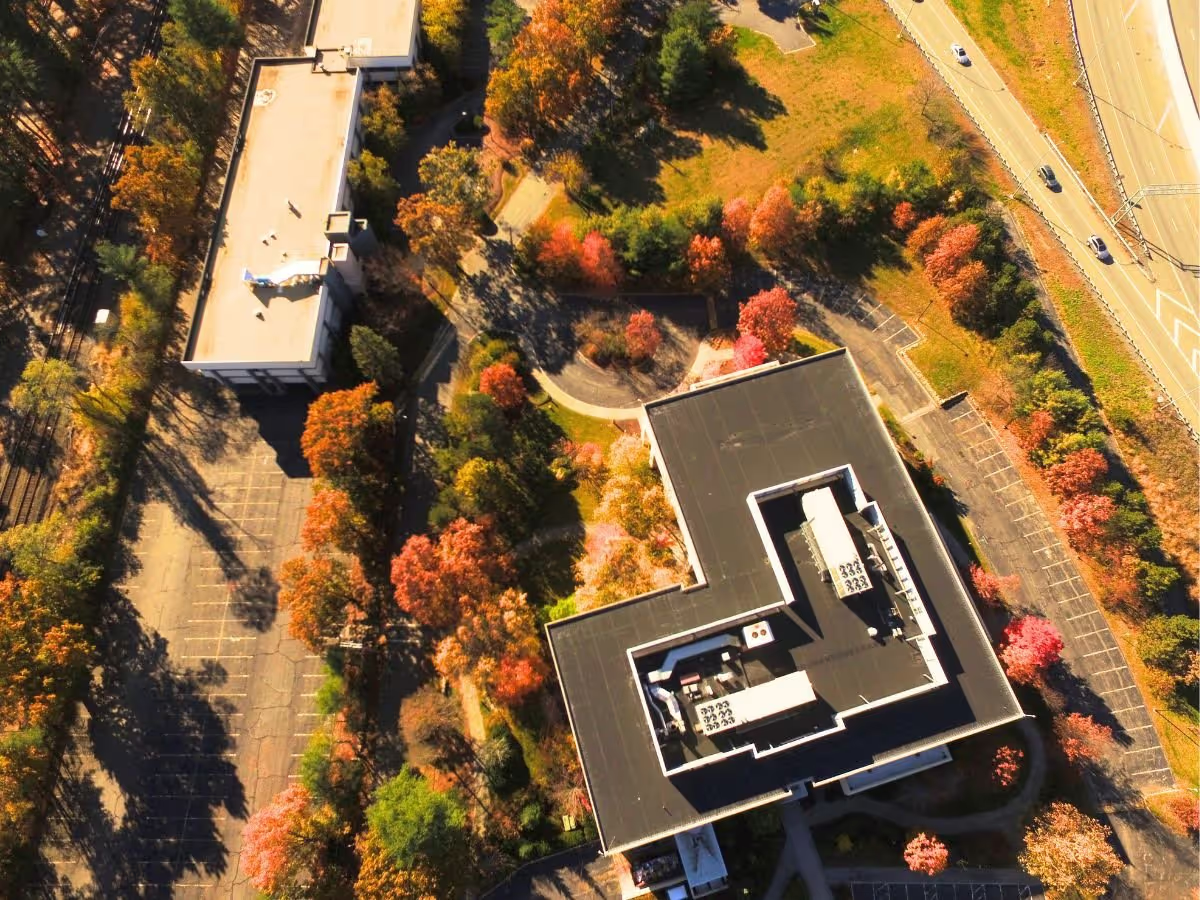
Partnering with Shawmut Design and Construction
Existing Conditions has a great partnership with Shawmut Design and Construction. They often engage us at different stages of a project's timeline. Typically, Shawmut tasks us with 3D laser scanning the current state of a building they've acquired. This allows them to compare the actual conditions against the construction documents or models they have, helping to identify potential issues early on for better coordination.
Shawmut selected Existing Conditions as their partner for the projects at 9 and 20 Riverside Road. These subsequent stages occurred following the completion of demolition work. In March of 2022, Existing Conditions was selected for the exterior documentation of 20 Riverside Road, and several months later, in June of 2022, Existing Conditions was selected for the interior documentation of 20 Riverside Road.
As stated by Joseph Lombardi, Senior Superintendent at Shawmut Design and Construction, “When considering what matters most in choosing a partner for this kind of work, it's clear that competitive pricing played a key role in our decision to work with you. Existing Conditions pricing not only fit within budget but also proved to be more competitive than other 3D laser scanning companies we've engaged with in the past. This, combined with the accuracy and reliability of the existing conditions model, set Existing Conditions apart as our preferred choice.”
Scope of Work Evolution
Pre-Demolition Scanning of Riverside Labs
Initially, in August of 2021, the project began with Gensler on a core and shell project, before any demolition had occurred and without Shawmut’s involvement. Our task was to 3D laser scan the building's exterior and identify key common areas. Having worked extensively with Gensler on various projects, including significant ones like One Post Office Square in Boston, Massachusetts, and several interior fit outs, we've established a strong relationship with them.
The Existing Conditions team conducted its 3D laser scanning field work in October and November of 2021. The scope of work at 20 Riverside Road was carried out with a variety of tools on site by Existing Conditions. The Leica RTC360 laser scanner was utilized by Existing Conditions to document the majority of the interior space. Additionally, the Leica ScanStation P50 was used to scan the perimeter and to integrate the survey control provided at both sites, including this building and the adjacent 9 Riverside Road project. Drones were also deployed by Existing Conditions to survey the entire campus, encompassing the two large buildings and all the parking lots, capturing the inner exchange between Interstate 95 and Pike 90.
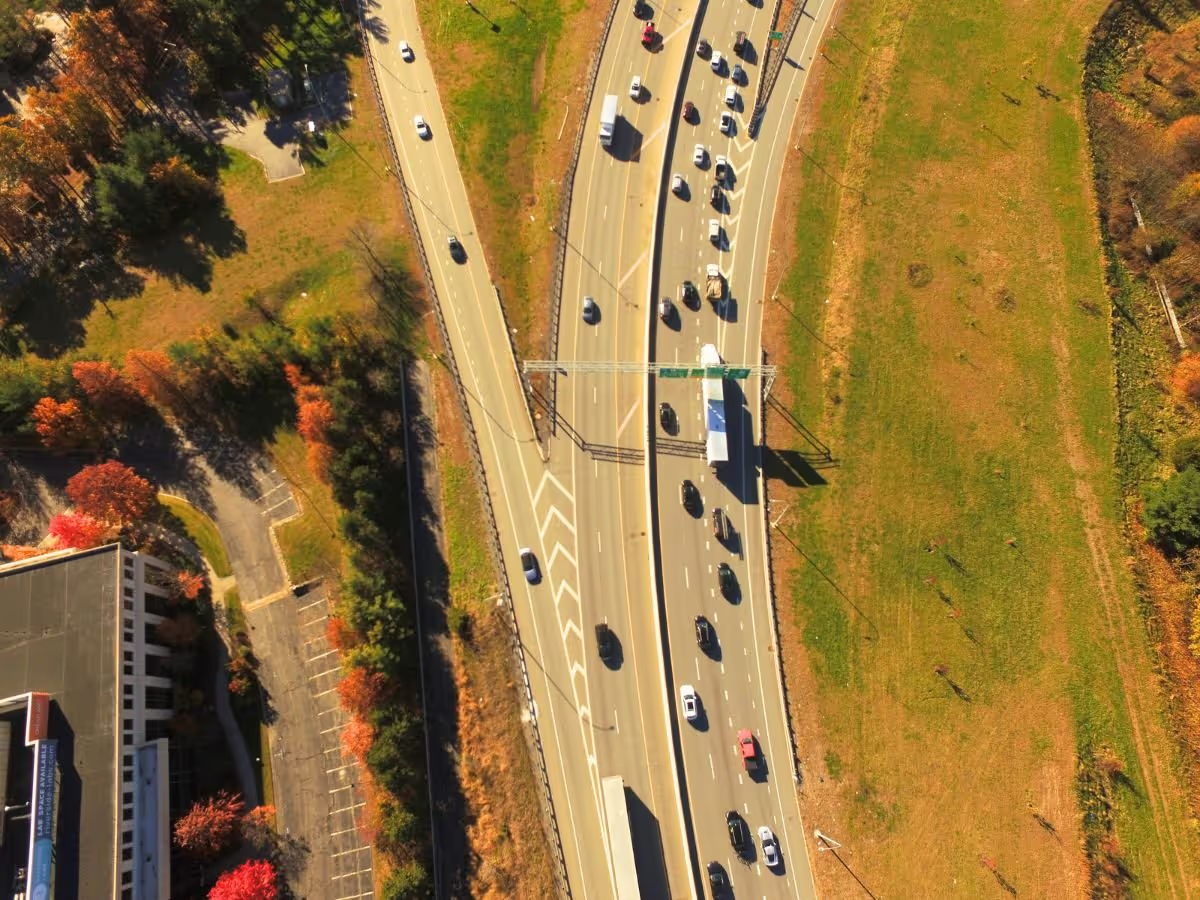
In the initial phase, focusing on the core and shell, Existing Conditions had three personnel on-site at various times, utilizing different equipment over four to five days in total. Our Operations Associate, Rich St. Pierre operated the Leica P50 laser scanner, while interior Leica RTC360 scans and NavVis VLX scans were conducted by Brian Ely, VP of Operations from Existing Conditions. Mike Remond, Existing Conditions' Operations Manager was responsible for additional Leica RTC360 scans. Joe Sullivan, our Senior Project Manager and Head of Drone Operations conducted the drone survey.
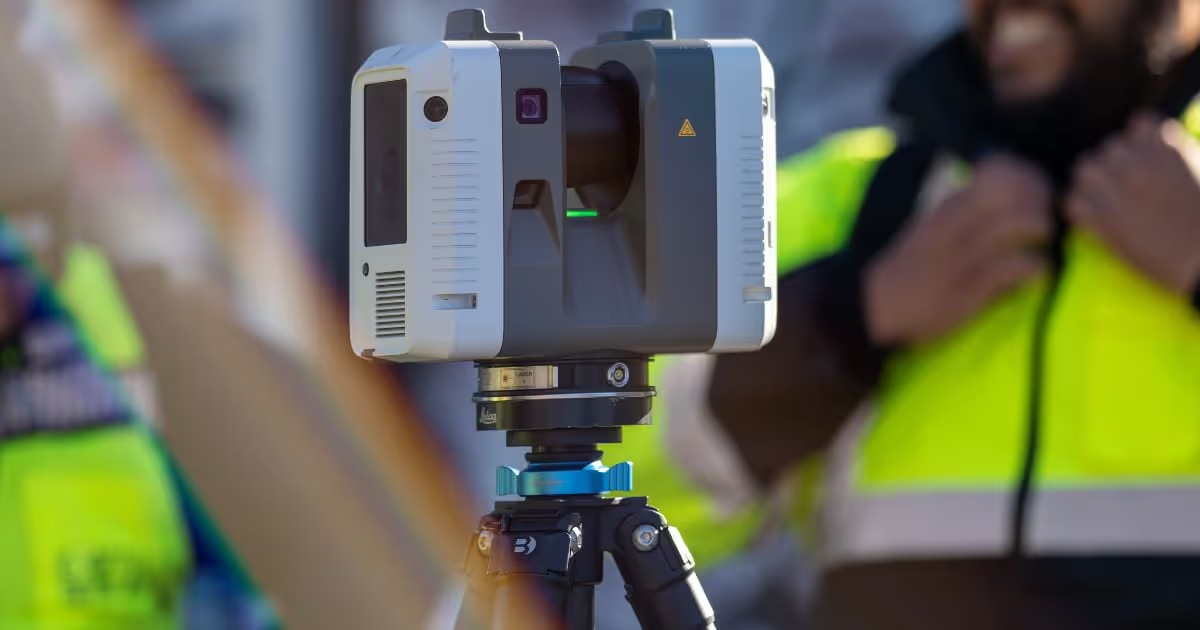
Post-Demolition Scanning of Riverside Labs
In April of 2022, Existing Conditions conducted our fieldwork beginning with the interior of 20 Riverside Road and extending to fieldwork at 9 Riverside Road in August of 2022. Existing Conditions followed a dynamic schedule for scanning the building, based on when each floor was prepared. As floors were completed, Existing Conditions received approximately a week's notice to prepare for scanning, aligning with the completion of demolition activities.
This advance notice allowed the team to ensure availability for on-site laser scanning. For each session, Existing Conditions utilized the Leica P50 laser scanner to establish control in the area and conducted Leica RTC360 scanning of the floors. Initially, the NavVis VLX was deployed before demolition activities, but post-demolition, the focus shifted primarily to using the Leica P50 and the Leica RTC360 for laser scanning.
By processing and creating 3D BIM models of each floor immediately after scanning, Existing Conditions was able to deliver these models to the client quickly. This approach allowed the client to begin coordination and construction activities on each newly prepared floor without waiting for the entire building to be scanned and modeled. This efficient process facilitated a seamless workflow, enabling the client to maintain momentum in their construction timeline without significant delays, even as the rest of the building was still undergoing demolition. Existing Conditions completed the project for Riverside Labs on November 2nd, 2022.
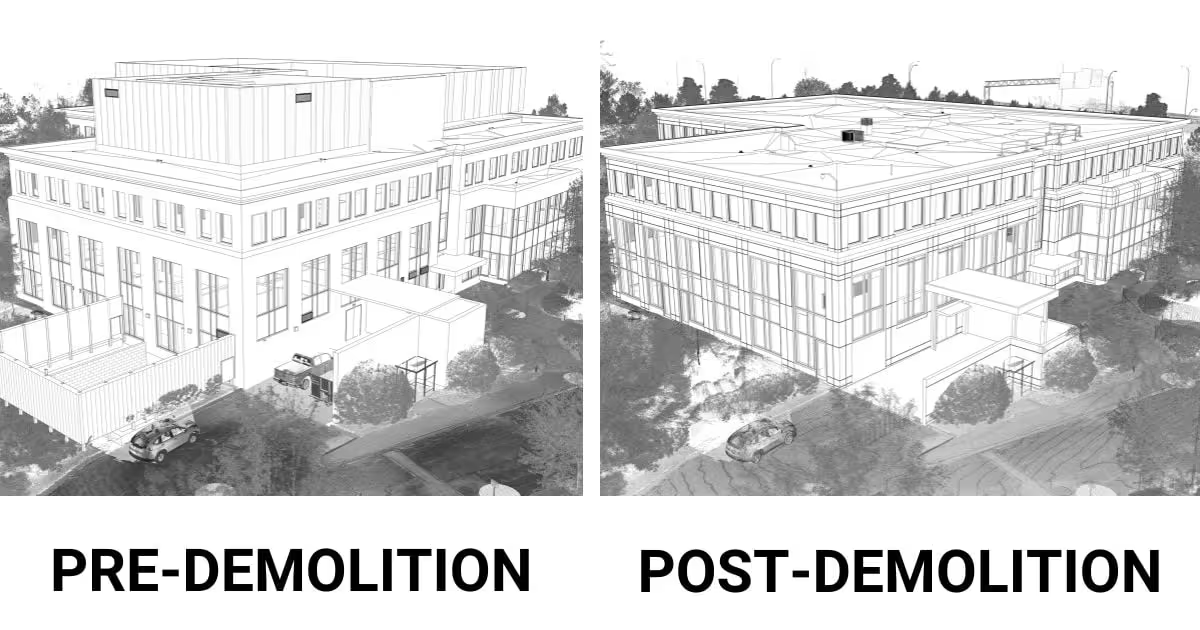
The Challenge
A significant challenge for Gensler at Riverside Labs was the availability of accurate and comprehensive digital as-built documentation. Initially equipped with only a basic set of 2D CAD drawings, the project lacked a detailed 3D Revit model, particularly for core and shell components. Our task was to create accurate, as-built drawings amd a 3D BIM model to prevent future hiccups, especially concerning MEP (mechanical, engineering, and plumbing) systems and structural placements that might change construction.
As the project advanced and Shawmut took over, following demolition, the focus shifted to verifying exposed elements such as specific MEP lines and structural components intended to remain. Shawmut had a limited amount of existing drawings and no pre-existing model to work from. The architecture team managed to create a preliminary 3D model based on some as-built drawings they found. However, for their purposes, especially for MEP coordination and steel design, Shawmut needed a more accurate representation. Shawmut’s goal was to have Existing Conditions incorporate all existing elements, such as roof drain piping and structural steel, which may have not been included in the initial architectural model, into their working model for better coordination.
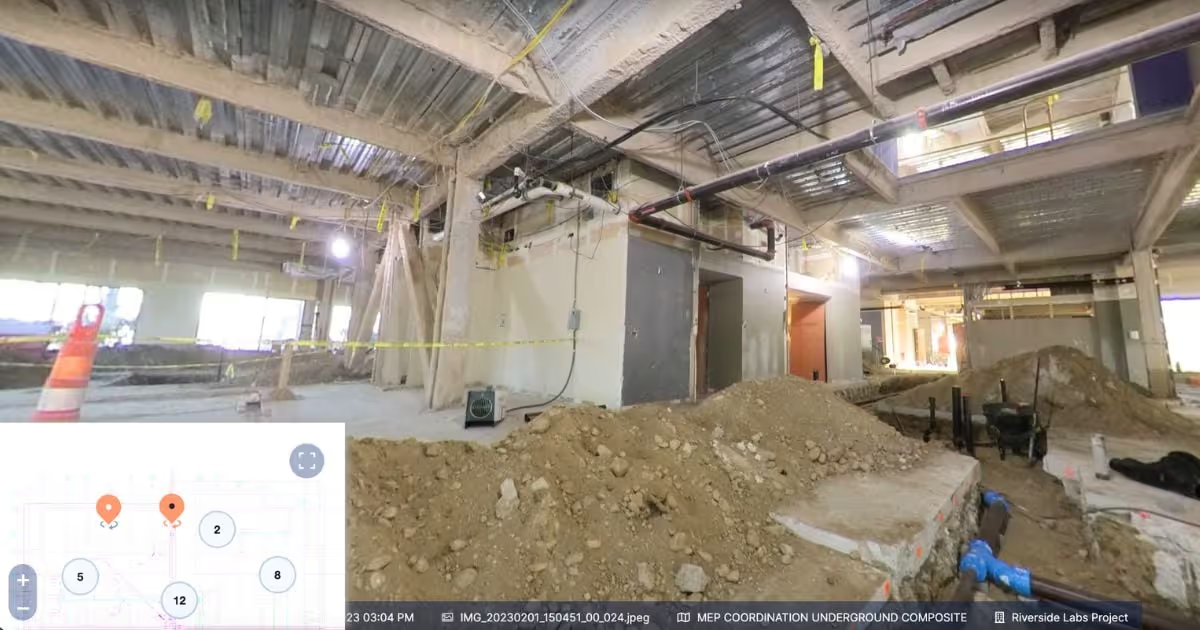
The Solution
Existing Conditions’ work with Shawmut frequently involves verifying the location of structural elements or MEP systems after demolition has exposed them. This step is crucial for ensuring that the integration of new components proceeds without any clashes or other problems. This approach to meticulous coordination and strategic problem-solving has been a key aspect of our successful collaborations in the past.
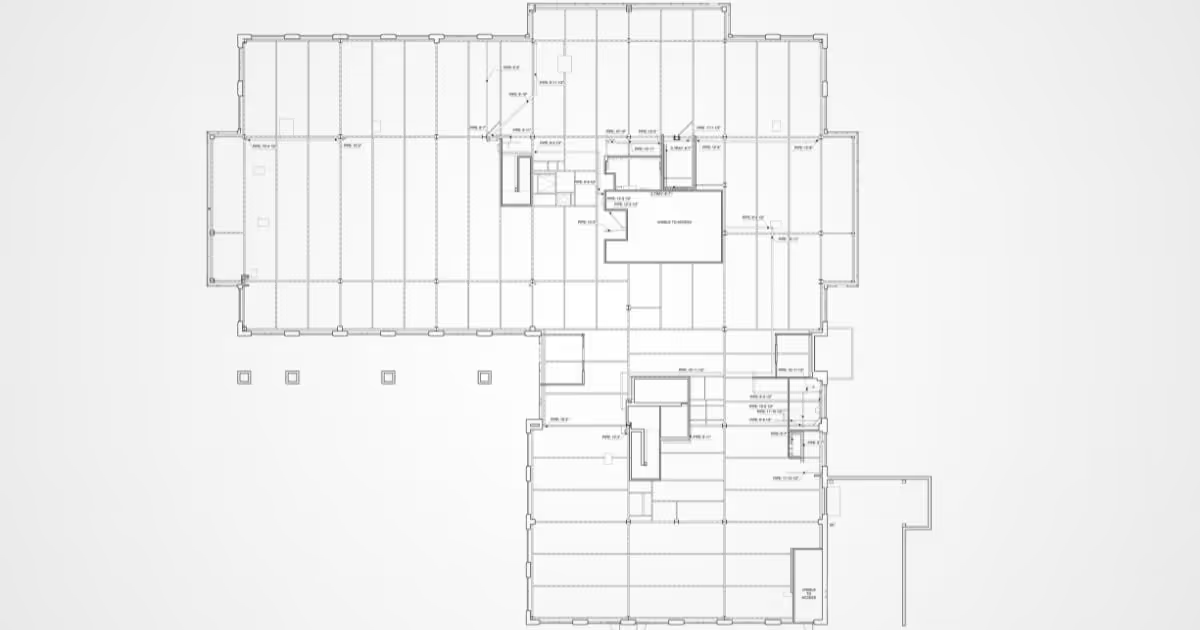
Secondly, 3D virtual walkthroughs significantly enhance design and construction processes by allowing designers to reference specific features not initially scoped, such as existing furniture layouts or floor undulations needing leveling, for more accurate material quantification like topping concrete. During construction, they are pivotal for detailed documentation, capturing MEP system installations before ceilings and walls are finalized, thus documenting the precise locations of pipes, valves, and switches efficiently. Utilizing tools like the NavVis VLX for comprehensive site capture, which requires only a day for data processing, offers a cost-effective way to create a building's digital twin. This digital twin is invaluable for the facility management team, enhancing building maintenance and management throughout its lifespan by providing situational awareness, facilitating better forecasting, and asset management.
After demolition was completed, and the remaining elements that were to be preserved, like certain structural columns, roof drain piping, and electrical heaters, were fully exposed, Existing Conditions was able to scan these elements. This allowed Existing Conditions to integrate all the steel beams and other structural components into a 3D BIM model, which significantly aided Shawmut’s mechanical instruction and coordination process. This step proved invaluable as it revealed numerous items present in the existing conditions scan and model that were absent from the architectural model.
Shawmut discovered that Existing Conditions’ 3D BIM model provided a significantly more accurate representation of the building's structure, including floor-to-floor dimensions and beam sizing. This precision greatly enhanced Shawmut’s coordination process with subcontractors, making it a crucial aspect of their project's success.
According to Joseph, “The service provided was exceptional, and the team demonstrated remarkable flexibility. They accommodated our needs by conducting multiple visits to scan the entire building comprehensively. As our demolition team worked through each floor, your operations team was adept at keeping pace, ready to scan the newly prepared areas. What set this service apart was the phased release of models; as soon as a section was scanned and modeled, we received a partial model to work with. This unique offering, not readily available from competitors, was immensely valuable and greatly appreciated.”
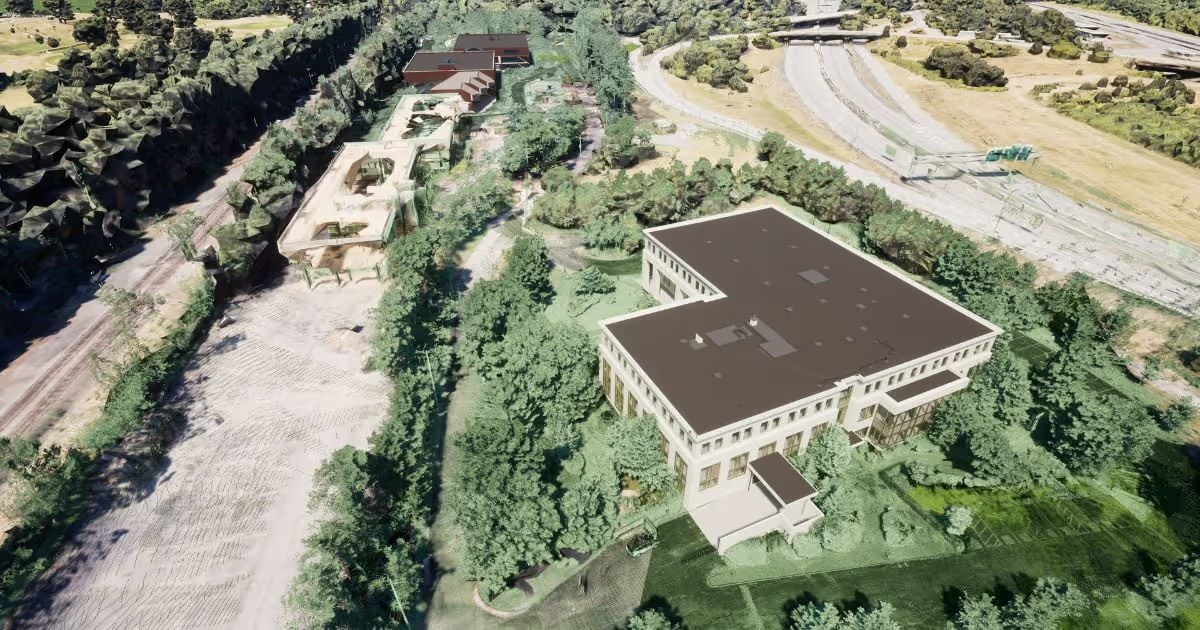
How This Project Was Unique
One of the standout features of this project lies in its comprehensive approach to documentation and coordination, both pre- and post-demolition. Before demolition, Existing Conditions collaborated with Gensler to create accurate as-built drawings, addressing the challenge of limited digital documentation and ensuring future construction proceeded smoothly. Post-demolition, the focus shifted to verifying and incorporating exposed elements such as MEP systems and structural components into the digital model, a task crucial for Shawmut’s coordination efforts. This dual-phase involvement showcases Existing Conditions' adaptability and expertise, providing invaluable support throughout the project's lifecycle and ultimately contributing to its success.
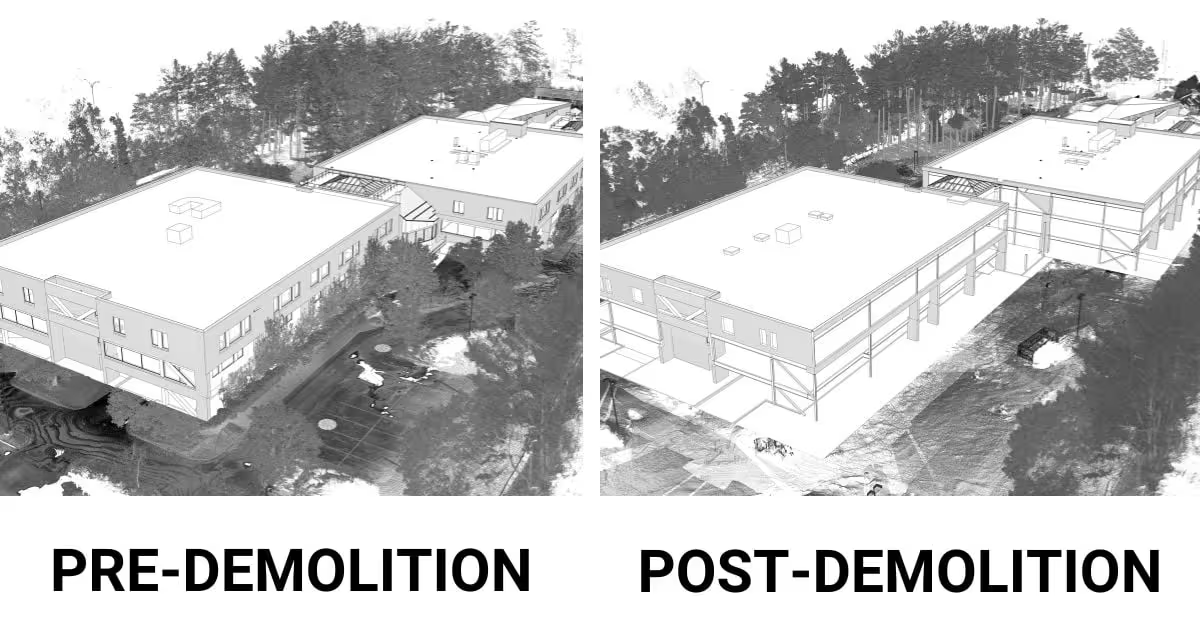
Joseph stated, “Existing Conditions has proven to be one of the top 3D laser scanning companies we've collaborated with, especially evident through our project at Riverside Labs. This positive experience led us to partner with them again for a more extensive and complex project at Harvard University. Their performance at Riverside Labs was a key factor in our decision to work with them at Harvard, to the extent that we did not seek quotes from any other 3D laser scanning companies. We directly chose them for our bid.”
Where Does This Project Stand Now?
Shawmut has achieved full coordination, and the installation of all steel components has been completed successfully. Shawmut’s model integrated seamlessly with their steel detailer's work, utilizing Existing Conditions’ 3D Revit model in their 3D detailing process. This synergy has significantly facilitated Shawmut’s mechanical coordination efforts.
Bldup reports that the first phase of Riverside Labs, featuring 90,000 square feet of lab space prepared for tenants, was finalized earlier this fall. ModeX, a biotechnology company in the clinical stage that is working on innovative multi-specific biologics for treating cancer and infectious diseases, is now utilizing 33,000 square feet of the building's space.
About the Client Shawmut Design and Construction
Shawmut Design and Construction is a $1.6 billion national construction management firm with a reputation for completing extraordinarily complex and logistically challenging projects. As a 100% employee-owned company, Shawmut has created a culture of ownership, proactive solution-making, and forward-thinking. Over eighty percent of its business comes from repeat clients, with a strong focus on building lasting partnerships. Shawmut has 10 offices, including Boston, Providence, Worcester, New Haven, New York, Los Angeles, and Miami.
Joseph Lombardi is a Senior Superintendent with Shawmut Design and Construction. Joseph enjoys using all the current technology available to assist with his day-to-day workflow and is an expert user of Bluebeam Revu and an avid user of CAD. Joseph has worked closely with Autodesk and their BIM 360 Field platform for QA/QC and coordination on large projects. All of Joseph’s document control is digital, including updating his drawing sets. Always having the most current information available on his iPad saves time in the field, and having the drawings at Joseph’s fingertips helps maintain a high level of quality on his job sites.
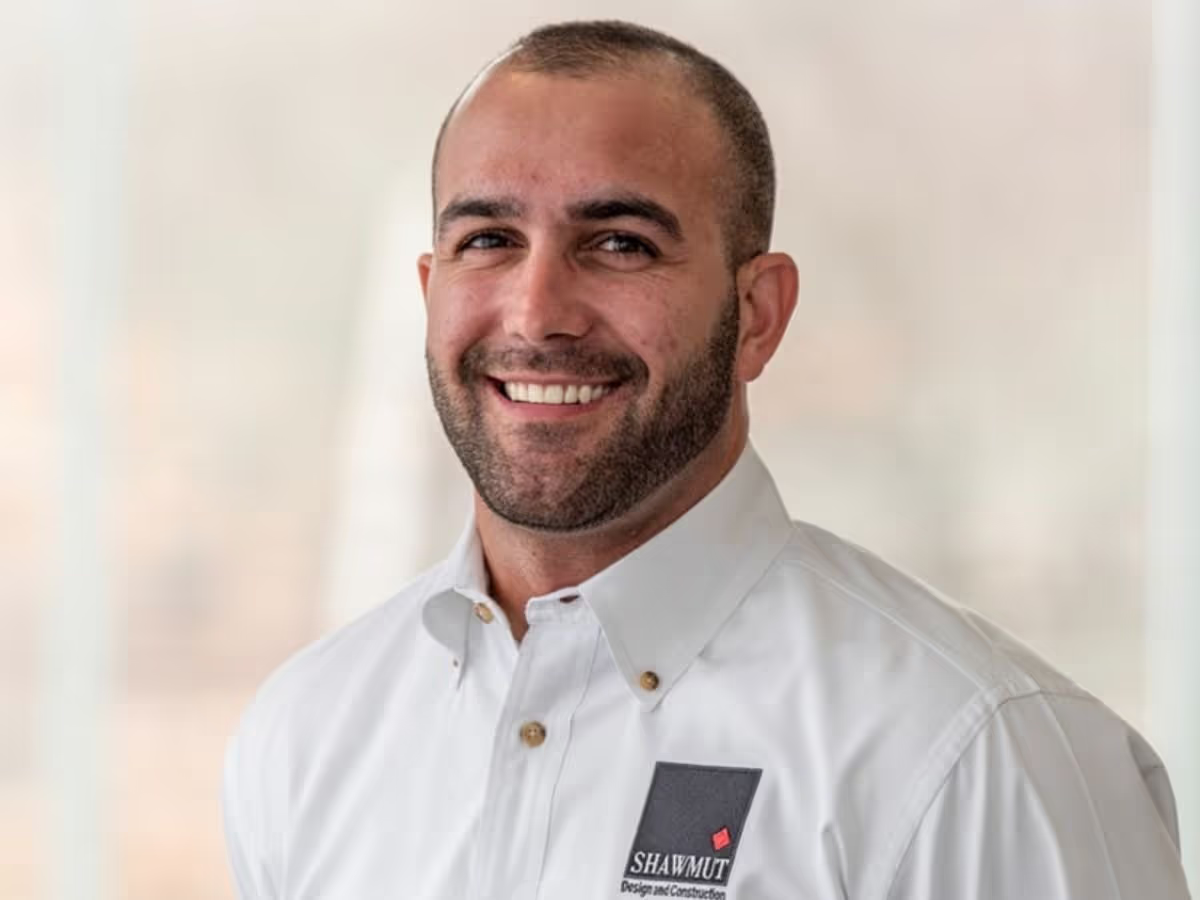
Existing Conditions 3D Laser Scanning Services
Over the past 27 years, Existing Conditions has measured, documented, and modeled over 10,000 buildings spanning over 700 million square feet across the United States, establishing ourselves as an industry leader in 3D laser scanning. Building professionals trust us to deliver digital representations of the as-built environment with unparalleled accuracy and efficiency. Our dedicated Project Managers provide fast and accurate 3D laser scanning services and drone imagery services, and expert CAD and BIM technicians create custom, detailed deliverables, including point clouds, 2D CAD drawings, 3D BIM models, 3D mesh models, TruViews, and 3D virtual tours. Our greatest reward remains delivering superior-quality scan-to-BIM work and knowing we played a vital role in our clients’ projects.
Ready to get started on your next project? Contact Existing Conditions today and let us be an extension of your team.
Related Case Studies
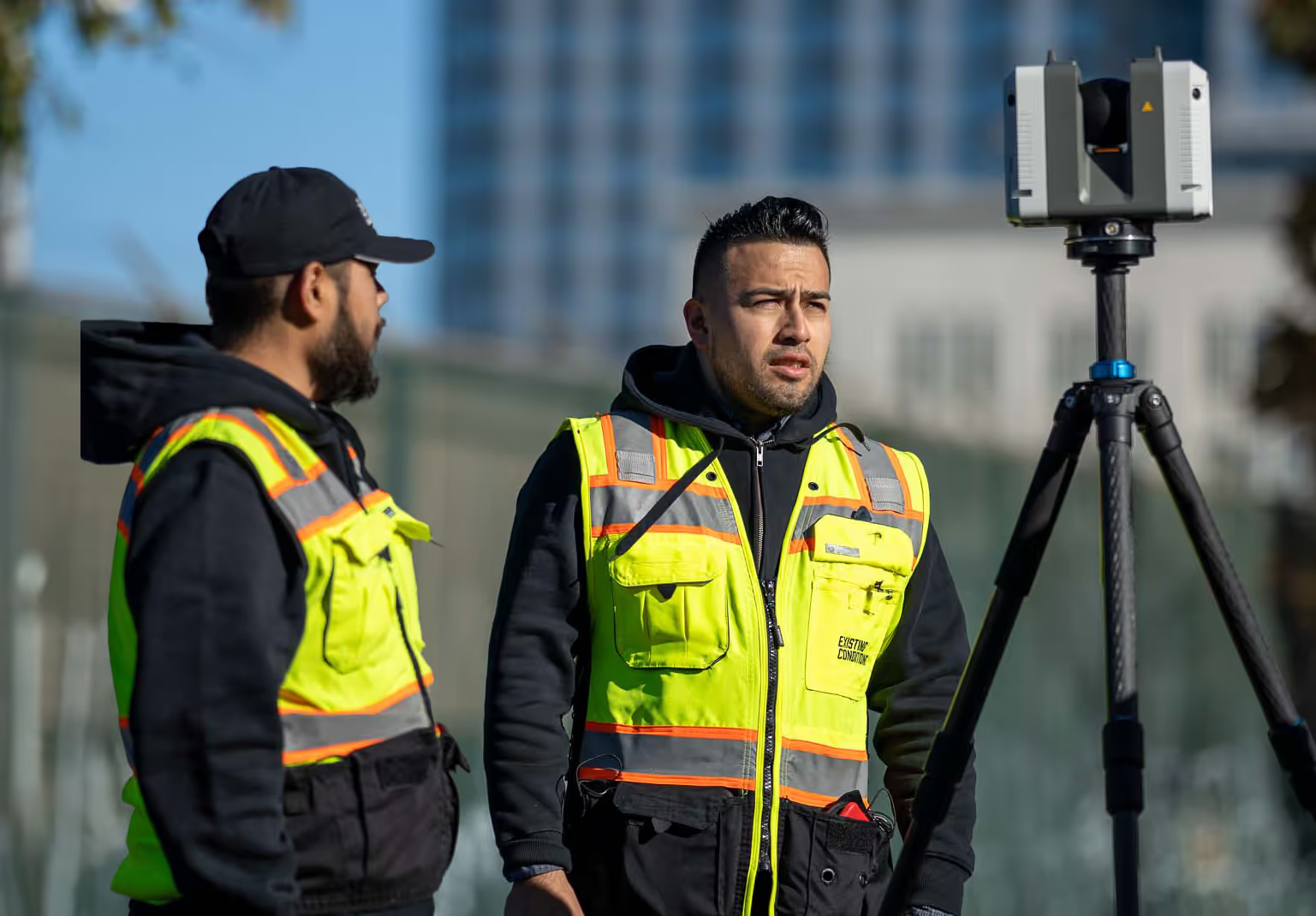